What is PDCA? A practical introduction for manufacturers
When you work in manufacturing, you’re no stranger to problems. Downtime. Defects. Inefficiency.
You’ll also be well aware that solving problems is hard if you don’t have a structure in place.
We often treat symptoms, not root causes. We don’t define clear goals. And there’s confusion about who should do what.
This course is designed to help you solve problems.
What is PDCA?
PDCA stands for Plan, Do, Check, Act.
It’s a four-step improvement cycle designed to help teams solve problems in a structured, repeatable way.
It’s a cycle because you’re always learning and improving.
Instead of guessing, you work like a scientist:
Plan: Define the problem and develop a solution.
Do: Test the solution on a small scale.
Check: Evaluate the results. Did it work?
Act: Standardize if successful or go back and try again.
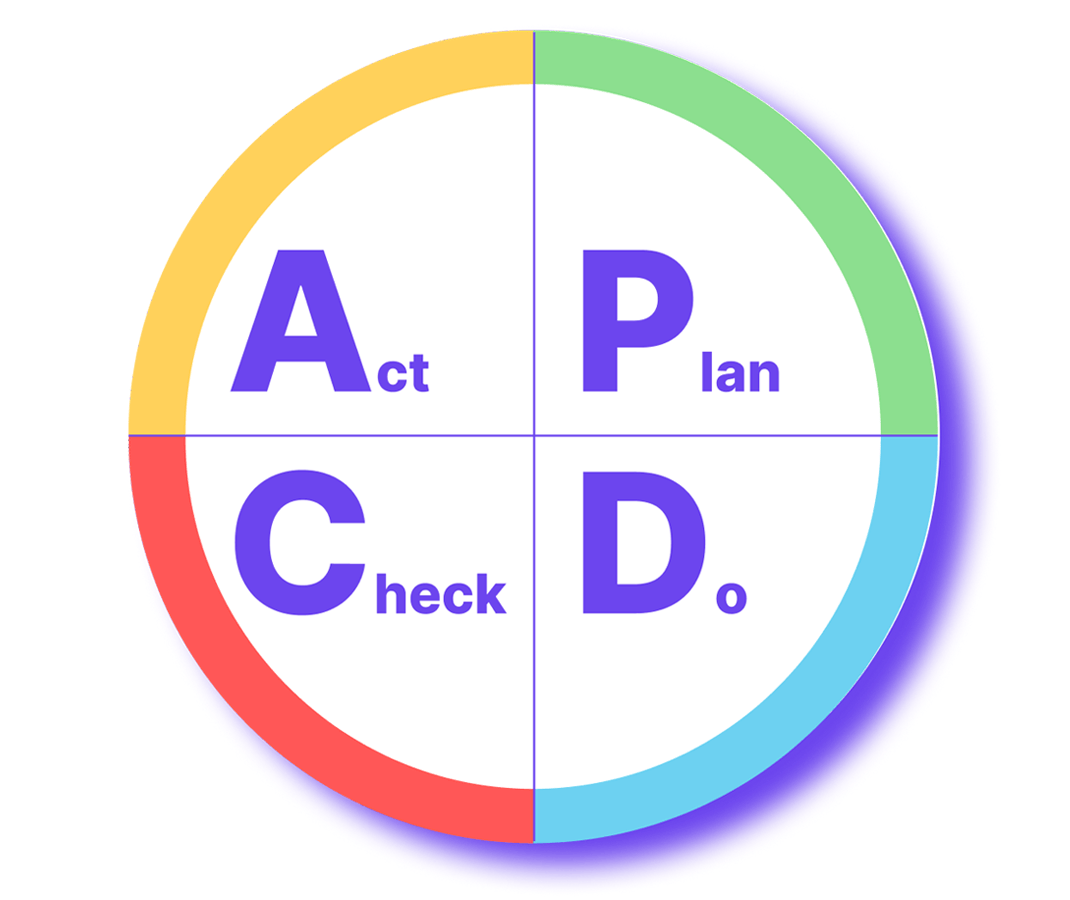
It’s not a one-and-done process. PDCA is cyclical because improvement is continuous. Every round helps you learn more and get better.
Why PDCA works in manufacturing
PDCA helps you fix the root cause, not just the symptoms.
And because it’s collaborative, it gets people involved in the right way: operators, engineers, managers, quality teams. Everyone works from the same playbook.
Here’s why manufacturers love it:
- It brings structure to chaotic problem-solving
- It’s easy to repeat and scale
- It encourages collaboration across teams
- It’s grounded in real data, not assumptions
You don’t need to be a Lean expert or Six Sigma black belt to use PDCA. It’s practical and simple.
When to use PDCA
We know that PDCA is an effective approach for problem-solving, but when and how should you actually use it?
You most likely don’t need it for everyday decisions, like choosing lunch. We can call these low-risk, simple problems.
But if you’re facing recurring issues, a complex challenge, or something that affects safety, quality, cost, or delivery, then PDCA is the right tool. We can call these complex and risky problems.
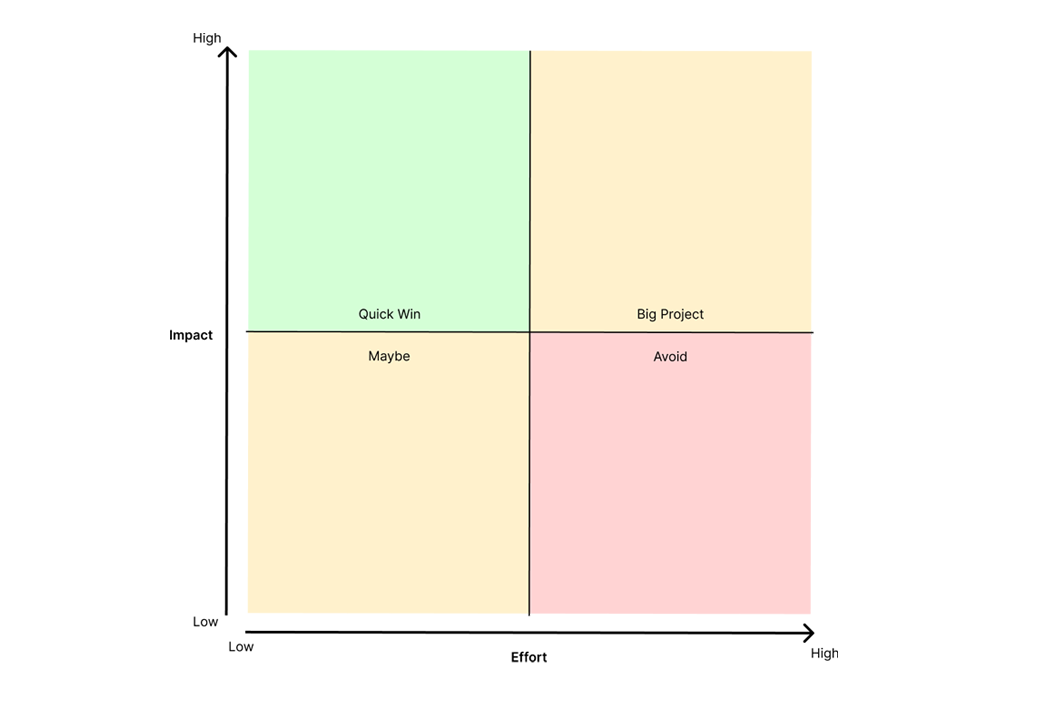
In short, you should use PDCA when:
- The root cause is unclear
- The issue keeps repeating
- Multiple stakeholders are involved
- You want to standardize a fix
- The problem affects cost, quality, safety, or delivery
As you will have noticed, these criteria make PDCA a great fit for manufacturing, where structure and repeatability matter.
The history of PDCA
Before we dive into how to use PDCA, let’s take a quick look at where it comes from.
The roots of PDCA go back to the 1930s and a statistician named Walter A. Shewhart, who introduced a method of iterative learning for quality improvement. He originally called it the Shewhart Cycle or Plan–Do–Study–Act (PDSA).
Later, W. Edwards Deming, who studied under Shewhart, adapted and promoted the cycle, often referring to it as the Shewhart Cycle in his early work. However, over time, Deming’s version evolved, and PDCA became the more widely recognized format that we know today.
Deming introduced the cycle to Japanese industry after World War II, where it was embraced and refined by companies like Toyota. Since then it has become a cornerstone of what we now call lean manufacturing.
That history matters. PDCA isn’t just a theory from a textbook. It has been tested, refined, and proven on factory floors around the world for nearly a century.
[CTA]
PDCA vs. DMAIC, 8D, and Kaizen
Before we go deeper into PDCA, let’s put it in context. It’s not the only problem-solving tool out there.
Here’s how PDCA compares to a few project management frameworks for problem solving:
8D stands for Eight Disciplines of Problem Solving. It’s often used in quality assurance, especially in the automotive industry. 8D walks through eight specific steps, including things like team formation, root cause analysis, and corrective actions. It’s detailed and structured, and great when you’re dealing with a recurring issue, especially one that affects a customer.
DMAIC comes from Six Sigma, and it stands for Define, Measure, Analyze, Improve, and Control. DMAIC is more data-driven than PDCA and is often used for complex problems where reducing variation is the goal. You’ll find it used heavily in large-scale process improvement projects.
Kaizen means “change for the better” in Japanese, and in manufacturing, it often takes the form of a Kaizen blitz, which is a focused, short-term event where a cross-functional team works intensively to improve a specific process. These events usually start with a clear goal and a charter. Then you walk the process, sometimes called a Gemba walk, to see the issue firsthand. The team maps the current state, identifies root causes, brainstorms improvements, tests them, and then locks in what works.
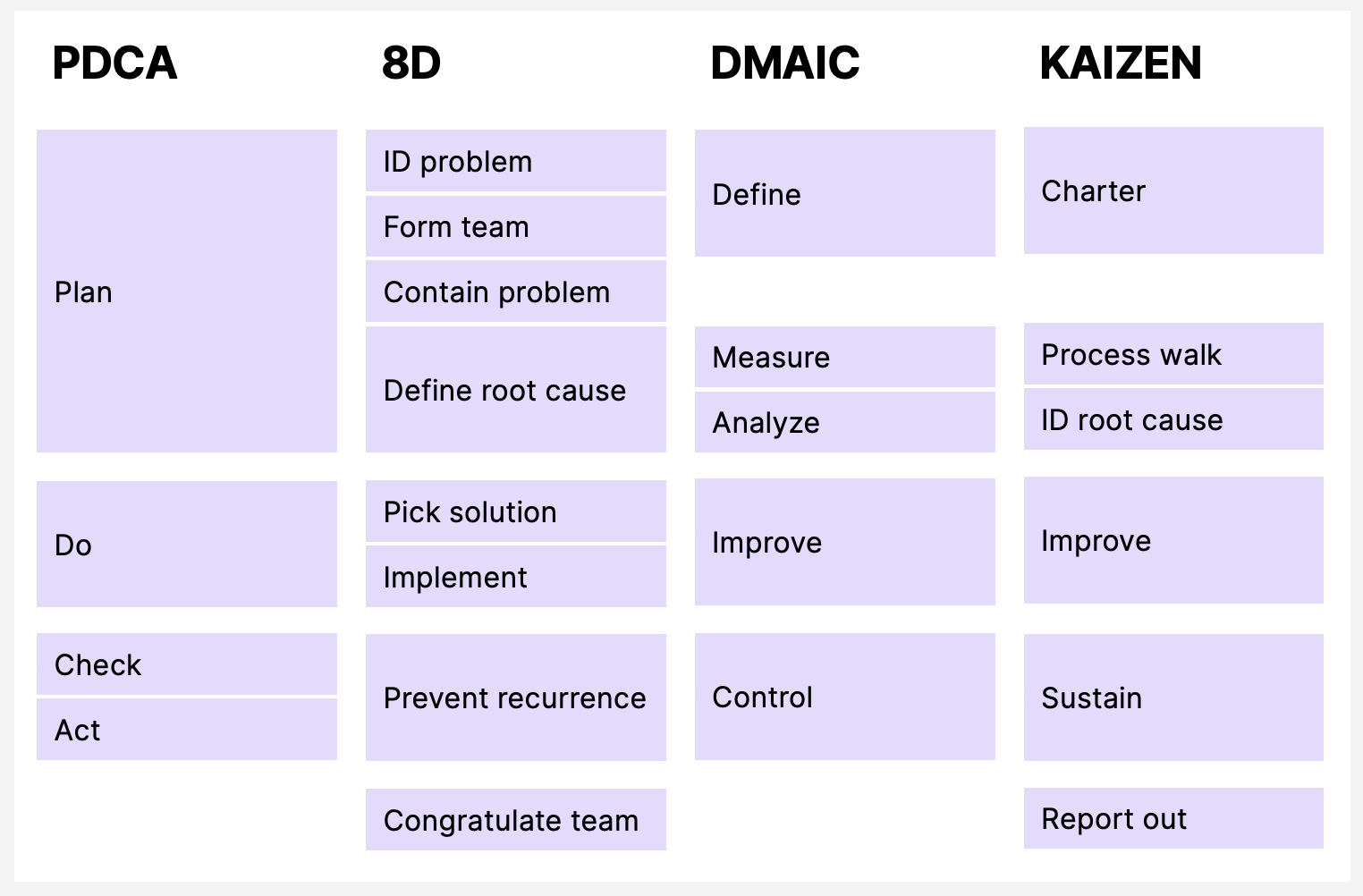
So PDCA isn’t the only option, but it’s often the best starting point and is incorporated into other methods. It’s simple, flexible, and it helps teams take action quickly without needing a consultant or a long training course.
Ready to try PDCA?
This was the first lesson in our PDCA course for manufacturers. In the next lesson, we’ll break down each step of Plan, Do, Check, and Act in detail.
In the meantime, if you’re ready to try PDCA yourself:
👉 Download our free PDCA template.
🎧 Listen to our podcast episode on PDCA.
💡 Or explore how you can track improvement digitally with Factbird Action Plans in our Knowledge Excellence App.