How Raymundos boosted their efficiency with real-time production data
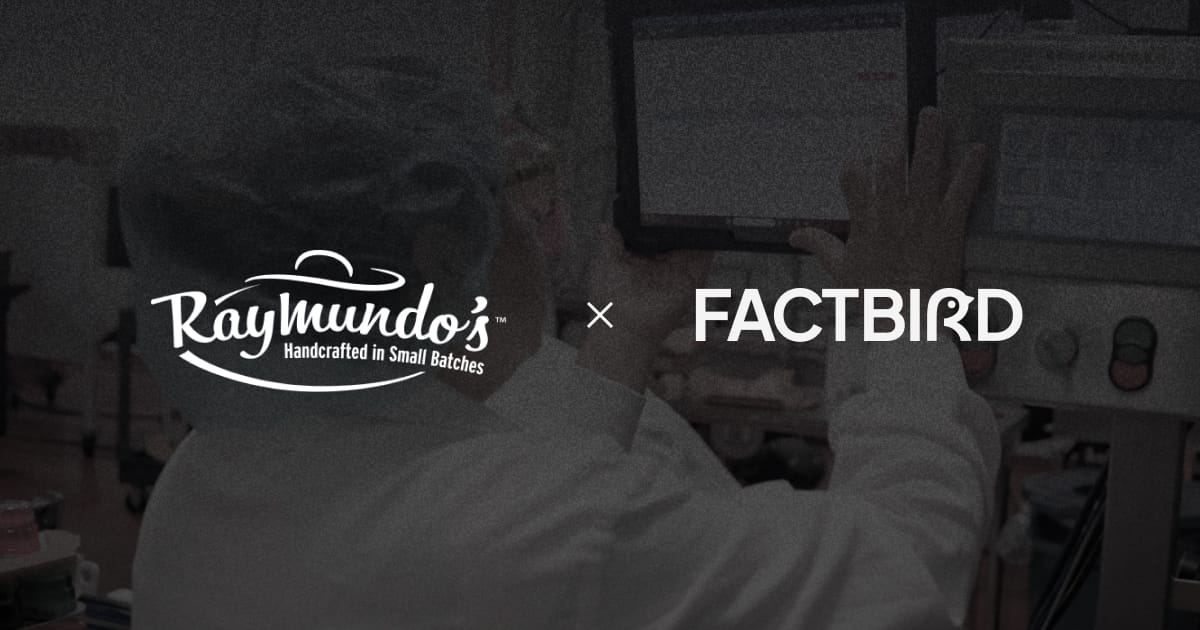
Meet Raymundos
Raymundos has produced authentic, ready-to-eat food products for over 15 years and understands the importance of using data to drive future success. They are a shining example of continuous improvement in the food and beverage industry, as well as success in creating delectable, best-selling desserts.
We went to see the Raymundos team in Bedford Park, IL, USA, to learn how they used the Factbird solution to achieve significant cost savings and output improvements.
Roberto Marquez, Plant Manager at Raymundos, oversees day-to-day operations, production, safety, quality, and maintenance. He spoke candidly with us about the challenges they faced and how they addressed those challenges with the help of Factbird's Manufacturing Intelligence solutions.
The challenge
Prior to using Factbird, most of the data collection at Raymundos was based on manual processes. Production data on losses was written down on napkins, paper notepads, and whiteboards, making it hard to keep track of production trends.
According to Roberto, “if someone didn't keep that piece of paper or someone would erase a whiteboard, all of a sudden, we didn't have information on what our losses were for the previous month or previous week. It was very day-to-day, and we couldn't strategically work on downtime solutions and continuous improvement ideas.”
Raymundos was aware that to keep up with rising raw material costs, labor shortages, supply chain issues, and competition, they needed to employ Industry 4.0 techniques. Digitalization of their data collection processes would allow them to gain more value out of their equipment, which is why they deployed Factbird.
The solution
Raymundos started incorporating Factbird into their processes in 2022. Today, Factbird has become an entrenched part of the day-to-day operations and a partner in the growth of Raymundos.
Today, everyone in the facility uses Factbird to document planned and unplanned downtime, stop causes, and specific information about downtime events.
Factbird is used across all lines
Raymundos uses Factbird devices, sensors, and cameras across all of their lines. They have deployed sensors at the front and back of their gelatin lines, on their packaging lines, and on their filling lines, for example.
Thanks to this plug-and-play digitization of their plant, Raymundos obtains real-time data on vital information, such as the total number of cases produced, the rate of cups filled, how active lines are, total production, and their productivity.
Implementation
Factbird was very easy to implement. For Raymundos, Factbird gave them access to an effective manufacturing intelligence system with minimal resources by connecting non-intrusive sensors to the cloud via secure IIoT gateways.
“It didn't require large servers. It was very easy to install. It was very easy to use.”
Roberto Marquez - Plant Manager, Raymundos
Apart from Factbird DUOs and sensors for data collection, Raymundos uses the following solutions:
- They have iPads on each line that operators use to register stops as they happen.
- They have performance dashboards on all of their lines. These give teams instant information on where they are tracking in terms of batch targets.
- Raymundos uses Factbird Views to assist with the identification of stop causes. Factbird VIEWs are cameras on key equipment that record stoppages and enable users to observe what went wrong with, e.g., packaging machines after the event.
- Finally, Raymundos uses a custom PowerBI executive report as their single source of truth for executive decision-making.
“The cameras are a great source of information to help us see why certain things are happening.”
Roberto Marquez - Plant Manager, Raymundos
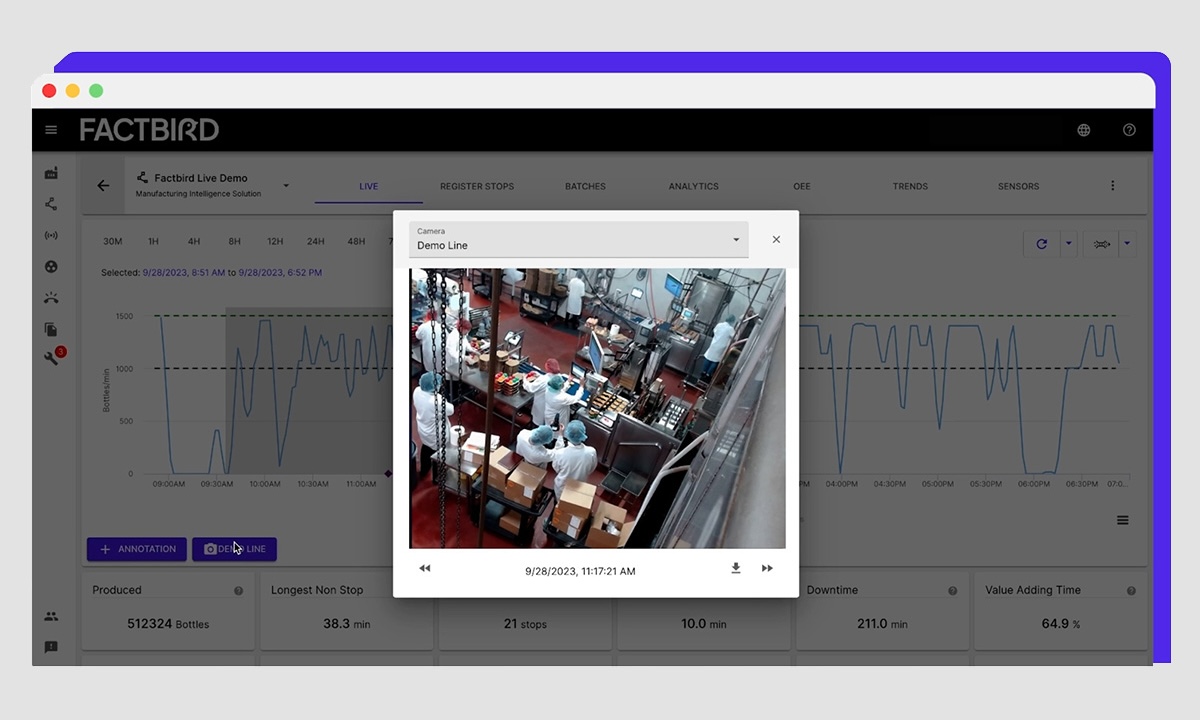
It took between three and five weeks to train teams in Factbird and align on expectations.
Buy-in was easy to get across the organization as the operators and the executive team quickly saw the benefits of Factbird’s production analytics.
The performance dashboard
According to Roberto, the Factbird performance dashboard is a great tool “for someone who has 100 things to do. It's a quick snapshot of exactly how well the facility is running. You can glance at it, see what asset is running, at what rate, and record downtime events.”
Roberto also appreciated that it was customizable to the information they wanted to see.
The shop floor performance dashboards give the Raymundos team relief to see that everything is going well, but they also provide information if something goes horribly wrong and allow them to focus their efforts on fixing it.
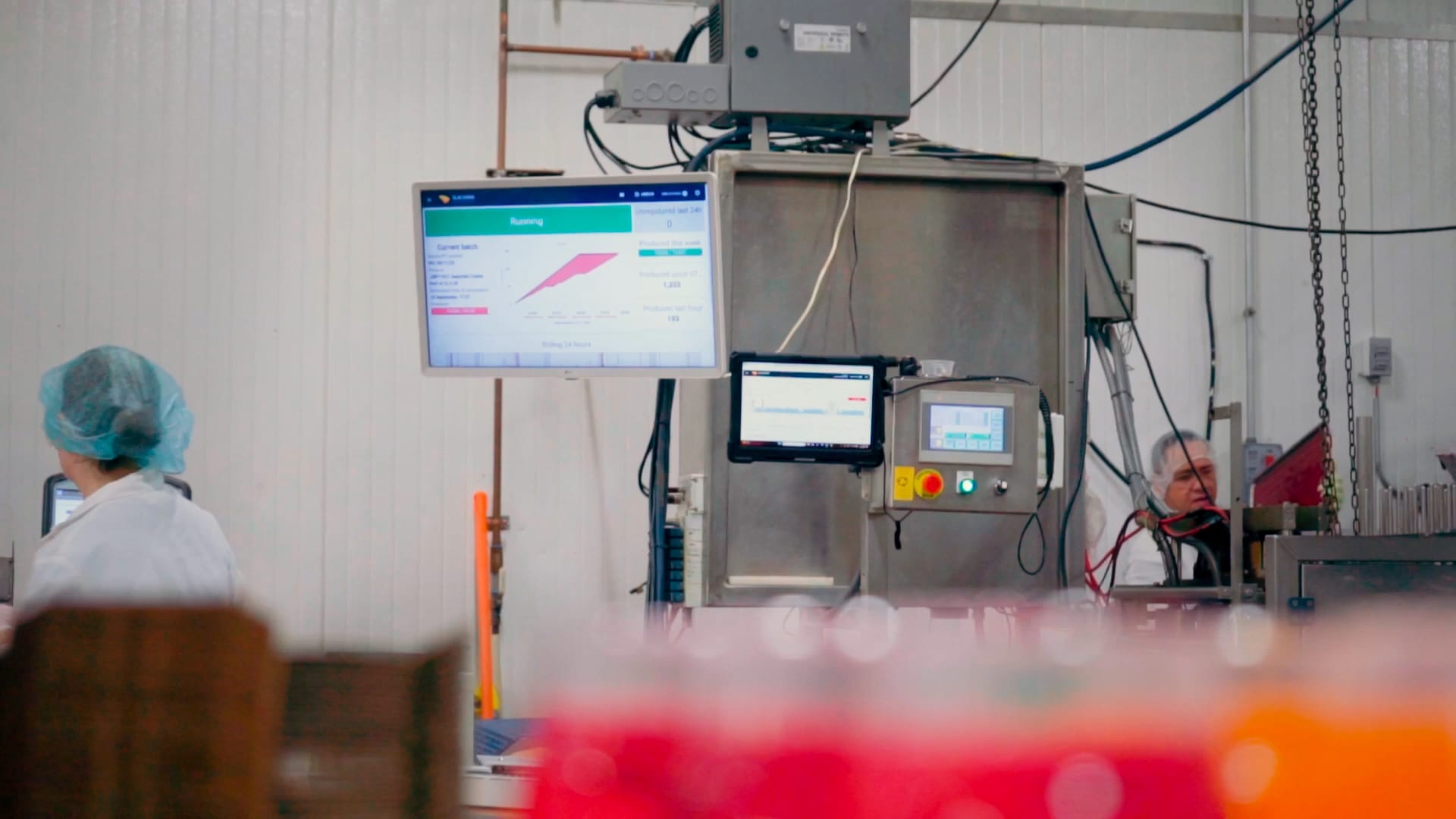
OEE is reviewed on a daily basis
In terms of workflow, one of the first things that Roberto implemented was using Factbird in his 8 a.m. production meetings. On a daily basis, they look at a 24-hour summary report that shares how each shift performed, including the cause of the biggest downtime.
During the meeting, they review all the downtime across all the lines and talk about OEE (overall equipment effectiveness). It gives the Raymundos team a quick snapshot of how effective the day was compared to the previous day, seven days, 30 days, and so on. That's a great piece of information for Raymundos, not only for the production team but also for their executive team to see how well the business is performing.
“We're able to see our performance increase day by day, week by week, month by month.”
Roberto Marquez - Plant Manager, Raymundos
Raymundos target for OEE is 95%, and if they don't meet that target, then they take immediate action by looking at what caused the losses.
OEE is communicated to the entire team, including how much total downtime there is and the root causes, and thanks to Factbird, they’re able to get all that information relatively easily.
The results
Raymundos is obliterating their previous production records. Their total cost per cup has gone down, and their case rate has gone up. These production KPIs are what drive costs, and by optimizing them, they are now more competitive and stronger in the market.
A 20-point jump in OEE
Raymundos OEE has gone up about 20 points across all their equipment since they began using Factbird.
Initially, when Raymundos started using Factbird's OEE Software, they were ranging between 60 and 65% OEE. Right now, they are averaging between 80 and 85% OEE.
“We’ve gone up about 20 points in OEE overall, across all of our equipment.”
Roberto Marquez - Plant Manager, Raymundos
It’s easy to track stoppages
Roberto highlighted that the sensors are great at identifying any type of speed loss.
Factbird's Production Insights app automatically prompts operators to record the reason for stoppages or speed losses. They are then able to use that information to effectively solve problems and dive into root cause and breakdown analysis.
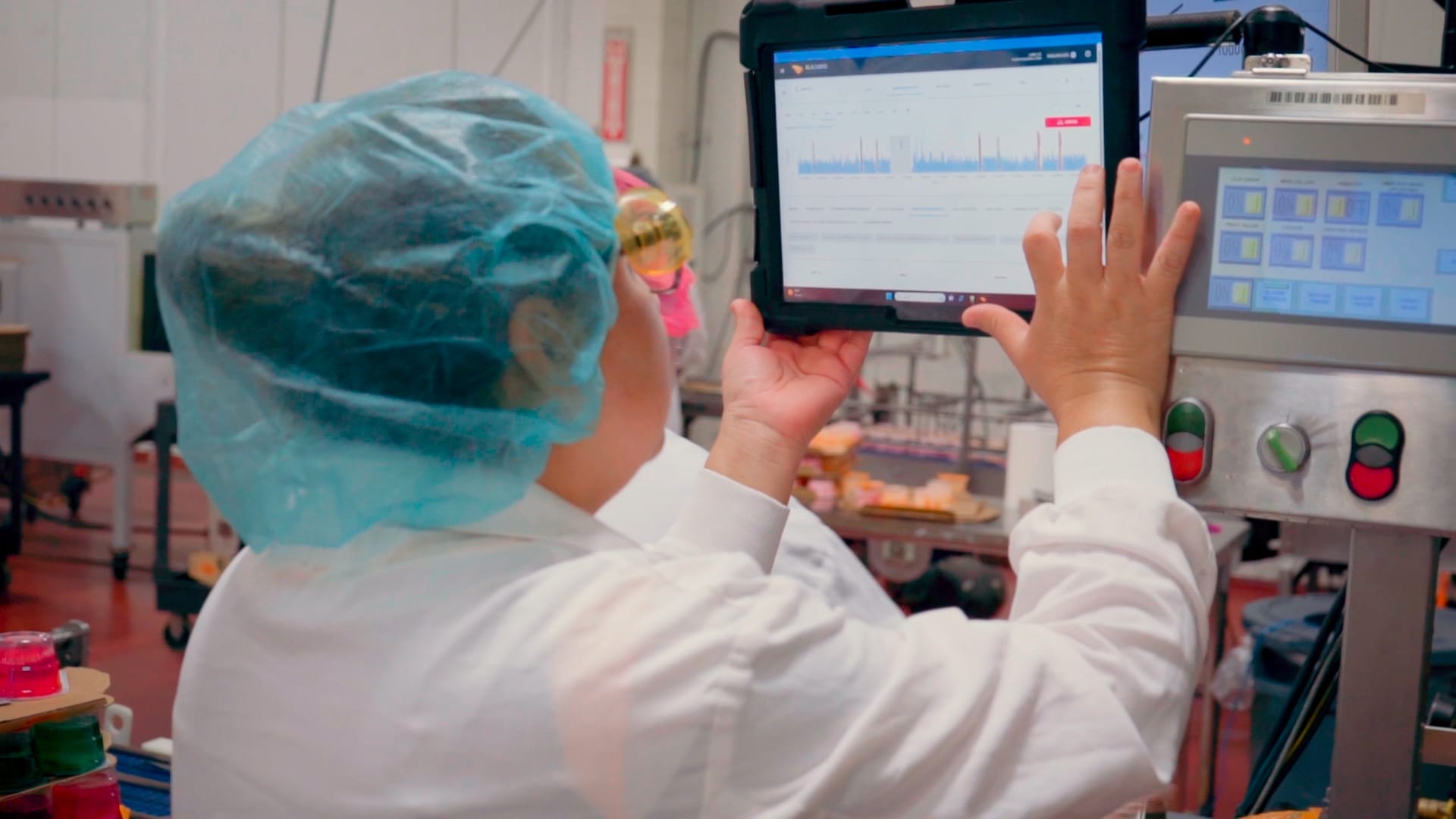
Actionable, live data
Factbird also gives the Raymundos team live information on how well the lines are performing. If they see that a line is not performing at rate or at target, they’re able to take immediate action and instantly see any changes to their case rate.
According to Roberto, “now that we're recording that data, we're looking at the trends, and based on where we're seeing losses, we're taking actions to be able to prevent the issue from hurting us again the following week or the following month.”
“It becomes very easy to identify, prioritize, and take action.”
Roberto Marquez - Plant Manager, Raymundos
A culture of improvement
According to Roberto, the Raymundos team “don’t want to struggle with the same thing over and over again. They know that if they continue documenting, we're going to see that data, and we'll be taking action. And when they come in in the morning, they look at their dashboard, and they see how the last batch went, which sets targets for their shift.
“They're very competitive. When they see the previous shift’s performance, they right away aim for more. So having that information visible for them is a huge benefit.”
Something every manufacturer needs
Roberto summed up the importance of manufacturing data well by saying, “If you're not precise, if you're not working on the right things, your resources and effort can go down the drain. You're spending time, you're spending money, and you're not seeing any type of benefit.
“But when you're able to precisely take action and fix the things that are wrong, you are able to drive improvement where you need to drive improvement. Then, all of a sudden, you start to see profitability, better productivity, and better quality. And the overall health of the business starts to go up and get better as well.”