How Royal Unibrew achieved a 14% OEE increase in a few weeks
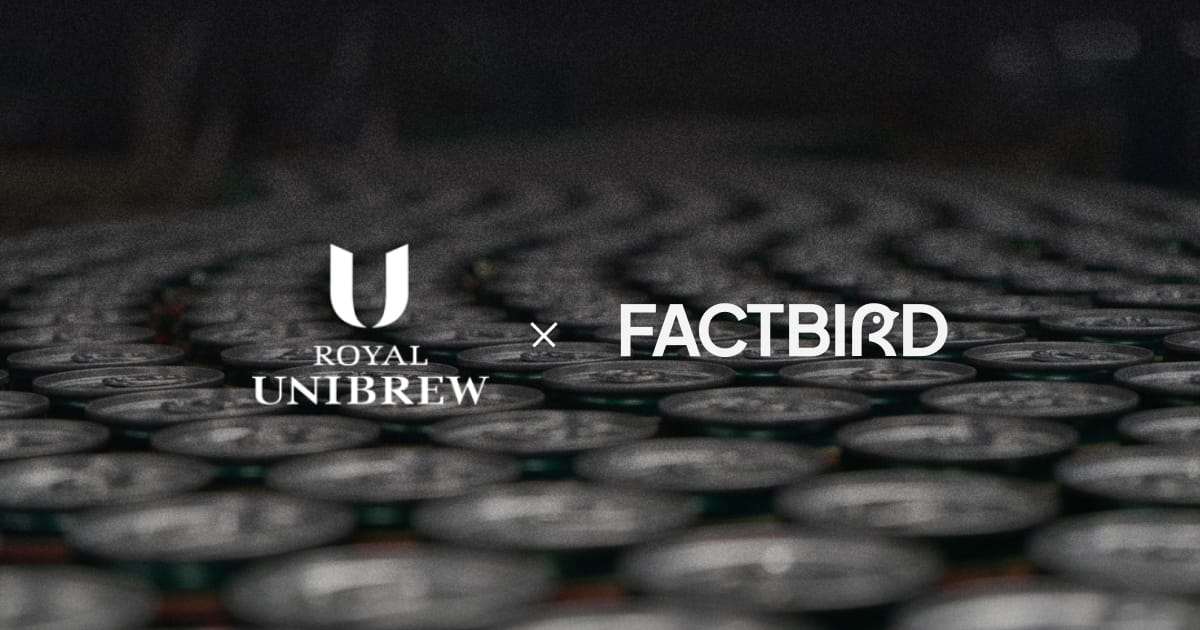
About Royal Unibrew
Royal Unibrew is an international brewery headquartered in Faxe, Denmark. Recognized as the second largest beer company in Denmark, with a strong presence in the Baltic countries. Brands included in Royal Unibrew’s portfolio are Faxe, Ceres, Royal, Albani, Vilniaus Tauras, and Kalnapilis.
Since 2018 they own Etablissements Geyer Frère, producers of the Lorina soft drink brand. Also, Royal Unibrew is in charge of brewing and marketing Heineken beers in Denmark.
Watch the video below to find out how Royal Unibrew quickly identified and eliminated issues using Factbird and increased Overall Equipment Effectiveness (OEE).
Challenges and Decision Making
Counting with different subsidiaries located in different countries makes the production monitoring process taxing, lacking a unified method to track manufacturing metrics and OEE across the company. In an effort to standardize processes, Royal Unibrew implemented Factbird to optimize its production lines. One of Factbird’s first applications was at Royal Unibrew, where they were facing the problem of a filling line running under capacity with a lot of stops on the line. There was a perception that if the line speed was increased, there would be more stops and thus less output.
Implementation Phase
Royal Unibrew installed Factbird IoT Gateways on the filling line and used Factbird's best-in-class OEE software. Within just two hours, the first Factbird unit was ready to monitor the output/hour data on a line where production capacity was below expectations. The installation was effortless and the line was able to run continuously while implementation was ongoing.
With the help of the data provided, Royal Unibrew received an overview of line speed and the length/location of the stops found on the line. Such detailed information is possible thanks to the sensors that provide live data per unit produced.
The data showed:
- How many bottles had been produced minute by minute.
- How many stops occurred, and how long each stop lasted.
After collecting data, it became clear that the line was not running at optimal speed. Optimizing adjustments were made to the line in order to increase the line speed to its expected value.
Intuition vs. Concrete Data
Royal Unibrew anticipated that an increased line speed would result in more stops which would lower the total production volume.
With real-time production data on hand, it was discovered that in most cases the number and the length of the stops were not connected by the increased speed of the line. Unibrew was therefore safely able to increase the line speed to its maximum capacity which increased output.
After this first successful usage of Factbird’s data, continued improvements on the production lines were pursued.
Enabling data-driven decisions
Factbird enabled them to be able to instantly confirm if changes or adjustments had the desired effect. Enhancement workshops were organized and improvements were continuously implemented on the filling line. Royal Unibrew was able to speed up the filling line while reducing the number of stops and making the line significantly more stable.
Factory-wide rollout
At Royal Unibrew's factory in Faxe, Factbird is used on all production lines to monitor line speed and stop causes. With Factbird’s stop-cause analysis tools, stops are continuously analyzed and problems are eliminated.
Performance Impacts
Monitoring and maintaining assets at the right time is critical for all manufacturing company. With help from Factbird, Royal Unibrew performs maintenance and replacement tasks with precise data insights.
Royal Unibrew also applied Factbird technology to optimize their production processes with eyes set on preserving its competitive edge.
With the reports provided by Factbird, both operators, and mechanics from Royal Unibrew started to test different adjustments to measure the effects in production time.
14% product line output increase after a few weeks
After a few weeks, issues found in the production line thanks to data were eliminated, impacting the line output with a 14% increase.
How Royal Unibrew uses Factbird
Here is how Royal Unibrew is continuing to use Factbird to focus is on keeping the process stable sand improving OEE:
- Ensuring standardized production line data collection across the factory where the Factbirds are installed.
- Having an overview of line speed and a stop cause monitoring due to real-time sensor data.
- Testing adjustments to production lines with the ability to measure effects in real-time.