How to structure improvements with PDCA
Manufacturing Matters Ep. 12
Dino Redzepovic, Senior Sales Engineer - EMEA at Factbird
Release Date: August 19, 2024

- Continuous Improvement (CI) is crucial for maintaining quality, cost, and efficiency in manufacturing.
- Plan-Do-Check-Act (PDCA)is a structured method for problem-solving and task management.
- PDCA can be applied in both simple task management and more complex problem-solving contexts.
- Challenges in CI include maintaining discipline, ensuring proper task definition, and keeping teams engaged.
- Factbird supports PDCA by helping teams identify, analyze, and monitor improvement activities.
In this episode of the Manufacturing Matters podcast, we explore the structure of continuous improvement (CI) efforts within manufacturing environments, namely on the four-step PDCA (Plan-Do-Check-Act) method for carrying out changes.
Continuous Improvement is essential for ensuring that manufacturing processes consistently meet the highest standards of quality, cost-effectiveness, and efficiency. Joined by Dino Redzepovic, Senior Sales Engineer - EMEA at Factbird, we dive into how PDCA serves as a powerful tool offering a structured approach to problem-solving and improvement.
What is Continuous Improvement?
Continuous Improvement (CI) refers to the ongoing effort to enhance products, services, processes, or production methods in manufacturing.
Whether it's improving quality, reducing costs, or optimizing delivery and performance, CI plays a pivotal role in maintaining competitiveness. Dino highlights the importance of structure in CI, emphasizing that without a defined framework, improvement efforts can become uncoordinated, leading to less effective outcomes.
What is PDCA?
PDCA is a cornerstone of the Lean methodology, providing a step-by-step framework for addressing improvement tasks. As Dino explains, each phase of PDCA plays a crucial role in structured problem-solving.
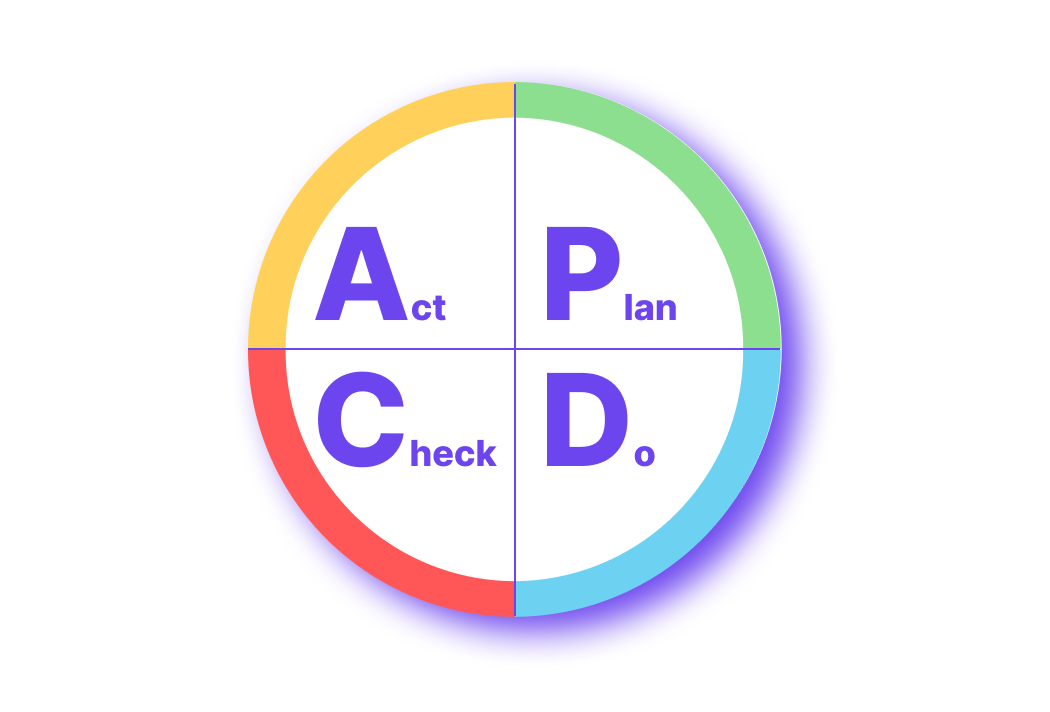
Plan: Identify the problem, propose a solution, and conduct root cause analysis. Dino stresses the importance of thoroughly understanding the issue at this stage, as it sets the foundation for the entire process.
Do: Implement the chosen countermeasure on a small scale to test its effectiveness. Test different hypotheses to see, especially, what would work best in the long term. This phase is about experimentation and learning.
Check: Evaluate the results using Key Performance Indicators (KPIs) or other metrics to verify that the solution works as intended over the long term.
Act: If the solution proves effective, finalize the process by updating Standard Operating Procedures (SOPs) and integrating the solution into broader operations. Conduct interviews and ask people whether they see the problem again to close off the process. This ensures that the improvements are maintained and applied consistently across the organization.
The importance of PDCA in manufacturing
PDCA is invaluable because it offers a structured approach to improvement activities, making it easier to track progress, align teams, and focus efforts on the most critical issues.
Dino mentions that without a framework like PDCA, CI initiatives can become chaotic, leading to disengagement and missed opportunities for improvement. He emphasizes that PDCA not only guides the improvement process but also helps in sustaining momentum, especially after initial easy wins have been achieved.
Application of PDCA in manufacturing
Dino discusses two primary ways to apply PDCA, depending on the maturity of an organization's CI practices:
1) Simple Task Management:
PDCA can be used as a guiding principle for categorizing and managing daily or weekly tasks on the shop floor.
Dino suggests that by assigning tasks to the appropriate stage of PDCA, teams can maintain a structured approach to task management, ensuring that each activity is aligned with overall improvement goals.
2) Systematic Problem Solving:
For more complex issues, PDCA can be combined with other Lean tools like the Ishikawa diagram, 5-Whys, or 6W1H.
Dino points out that in this context, PDCA serves as a systematic problem-solving tool, often employed in project-based CI activities with dedicated resources. This approach allows organizations to tackle more significant challenges in a structured and efficient manner.
Challenges and tips for implementing PDCA
Working with PDCA and CI in general can present several challenges. Dino shares insights into overcoming these obstacles.
Task management discipline: Ensuring that tasks are properly defined and tracked is crucial for success. Dino emphasizes the need for clear definitions and manageable tasks to keep the process moving forward.
Team engagement: It’s essential to involve the right people at the right stages and maintain momentum after the initial kick-off and early successes. Dino advises using strategies like visual management, such as a cylinder for collecting completed task Post-It notes, and competition between teams to keep engagement high.
Maintaining momentum: As Dino explains, after some time using PDCA, identifying new improvement opportunities can become more challenging. He suggests relying on data to guide further improvements and ensuring that new team members are adequately trained in the PDCA methodology. Remember to emphasize that every improvement is a good improvement.
How Factbird supports PDCA
Factbird complements the PDCA methodology by providing the data foundation necessary for effective CI.
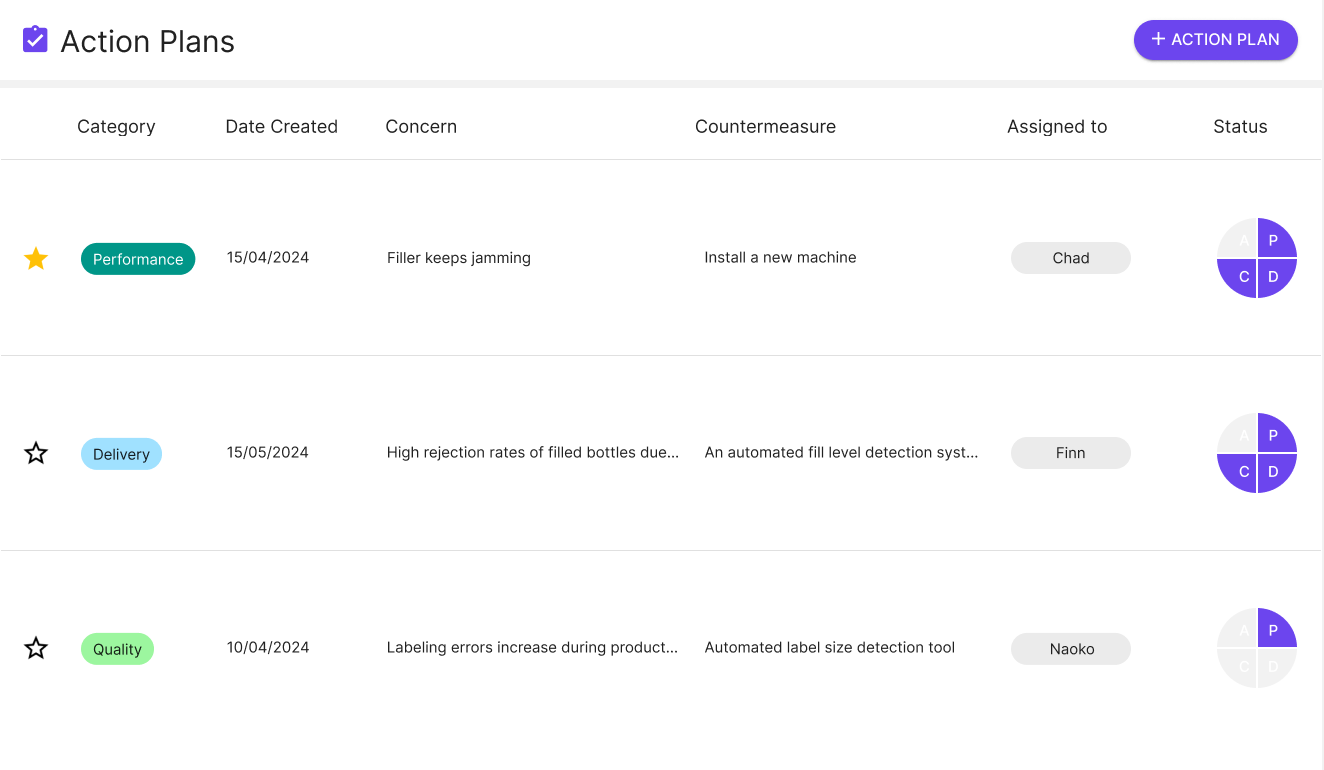
From identifying potential problems to conducting root cause analysis and monitoring the impact of implemented improvements, Factbird's tools enhance every stage of PDCA.
Action Plans in the Factbird Knowledge Excellence App help teams store, track, and reference PDCA improvement activities in the same place as the data collection and analysis is made. Here’s a quick overview of the benefits of using Factbird’s Action Plans:
- Get everyone on the same page with data-driven improvement activities across departments.
- Digitize problem-solving tasks and continuous improvement activities for more visibility and efficient task management.
- Preserve problem-solving expertise in the cloud to avoid knowledge loss and increase efficiency across sites.
- Creating a database of PDCA activity knowledge that will provide your business with useful training data for upcoming AI-assisted improvement tools.
If you’d like to find out more about Factbird’s Action Plans feature, you can book a no-obligation demo here: Book a demo.
Download a free PDCA template
We've created a free PDCA template for you to help you on your continuous improvement journey.
You can download the PDF template in A4 and A3 formats via our blog:
Free Plan Do Check Act (PDCA) template
Conclusion
Implementing structured improvement methodologies like PDCA is crucial for sustaining continuous improvement and maintaining competitiveness in today's manufacturing landscape. Dino's insights highlight the importance of having a disciplined approach to problem-solving, task management, and team engagement, all of which are essential components of a successful CI strategy.
By integrating PDCA into your operations, you can systematically address challenges, drive meaningful improvements, and ensure that gains are sustained over the long term. Tools like Factbird further support these efforts by providing the data necessary to identify, analyze, and monitor improvement activities effectively.
For more insights and practical tips on continuous improvement, lean manufacturing, and other industry topics, stay tuned to Manufacturing Matters. If you have any questions or topics you’d like us to cover, feel free to reach out to us via LinkedIn or email.
And remember to subscribe to Manufacturing Matters to get notified when the next episode is available on Spotify, Apple Podcasts, YouTube, Amazon Music, and other popular podcast directories.