Change management advice for manufacturers
Manufacturing Matters Ep. 7
Zoe Karasch, Sales Manager for the DACH region, Factbird
Release Date: May 27, 2024
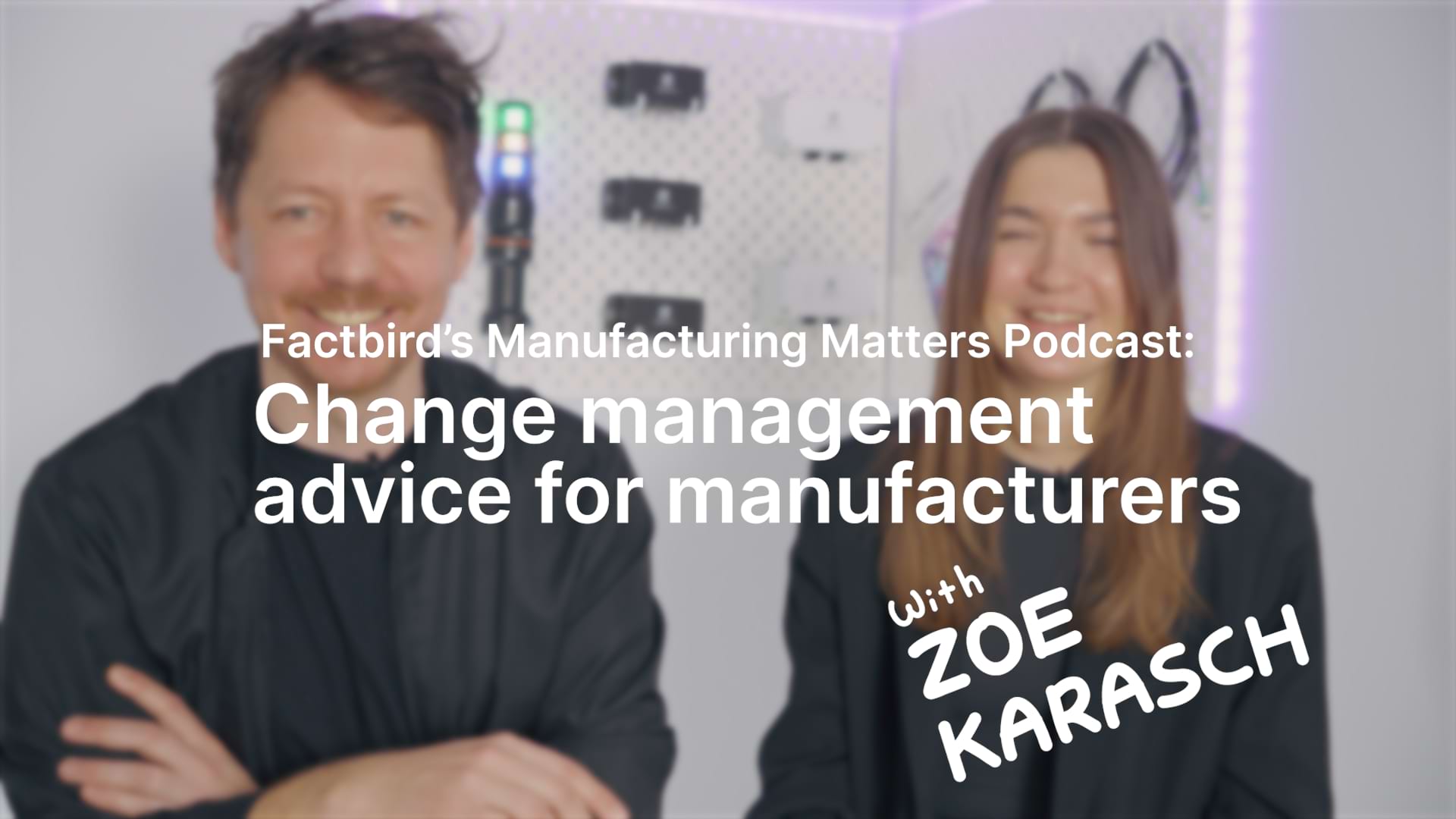
- Introducing new technology to manufacturing operations is transitional change.
- Good communication practices are essential.
- Map stakeholders and keep all affected roles involved.
- Maintain transparency without overwhelming colleagues.
- Incentivize engagement with new systems through bonuses and recognition.
Change management is a topic that comes up time and time again when talking about the implementation of new production monitoring systems. So, in this episode, we delve into practical strategies for facilitating change management in manufacturing operations with Zoe Karasch, Sales Manager for the DACH region at Factbird.
Zoe has an impressive background, working with both large and small manufacturers to enhance processes, reduce waste, and boost productivity. So let’s tap into her first-hand experience training organizations in OEE systems and production monitoring in general and get some helpful advice for change management.
Understanding Change Management
Change management is a structured approach to transitioning individuals, teams, and organizations from a current state to a desired future state. It involves preparing, supporting, and helping employees adopt change in order to drive organizational success and outcomes.
There are three generally accepted categories of change:
1) Developmental change
- Gradual change that improves what is currently being done.
- For example, improving existing skills, processes, methods, and performance standards.
- Typically, the goal is to increase sales or quality, interpersonal communication skills, problem-solving abilities, and development like that.
2) Transitional change
- Replacing an existing system, process, or strategy with new ones.
- Happens in a specific time period.
- The outcome is predictable.
3) Transformational change
- Introducing a completely new structure with lots of uncertainty.
- Complete change in identity of an organization.
- Nokia changing from television to cell phone manufacturing, for example.
- The outcome is uncertain.
In Zoe's words, change management is about getting people to accept and embrace change instead of resisting it. She emphasizes that while change is constant, it is not always welcome, making effective change management crucial for smooth transitions, especially in manufacturing, where changes often involve new technology and processes.
Key Strategies for Effective Change Management
Transitioning from paper-based or Excel-based systems to fully digital, live-data systems is a typical form of transitional change in manufacturing. Digitalization and the implementation of new manufacturing intelligence solutions are significant changes that require robust change management processes to avoid waste and ensure successful implementation.
During the podcast, we discussed four key pieces of advice for better change management.
1. Good Communication Practices:
Communication is the cornerstone of effective change management. Zoe emphasizes the importance of clear, consistent, and transparent communication throughout the change process. It's crucial to articulate the reasons for the change, the benefits, and the impact it will have on everyone involved. Regular updates and open channels for feedback help in reducing uncertainty and resistance.
In our case study on Wozniak Industries, Lorne Day, VP of Operations, has some good thoughts on effective communication and change management. Here’s some of what he had to say:
“If you have the tool and you just look at it, not asking questions, behavior is not going to change. Behavior only changes when you ask questions.
“Every penny I spend on any asset, and this is an asset, it’s about ROI, right? And it initially came across that this is something that Lorne wants to do, and that's the wrong thing. I probably presented it wrong. This is a tool that we need to be successful, to keep these doors open.
“So this is our tool, not my tool. That's the culture you have to shift on. You have to get buy in. It's all about the why. Everything's about the why.
“People don't mind change, they just mind being changed. And so this is a change in behavior. This is now holding leadership accountable. It's not necessarily holding the operators accountable. It's holding leadership accountable for doing the process that you put in place and using the data.”
2. Mapping and Involving Stakeholders:
Identifying and mapping stakeholders is a critical step. Zoe shares that involving key stakeholders early in the process ensures that their concerns and suggestions are considered before they grow into larger issues.
Know the answer to the “What’s in it for me?” question early. Engagement with personnel affected by change and understanding their perspective help foster a sense of ownership and commitment to the change, moving people towards intrinsic motivation as opposed to extrinsic, less effective motivation.
Engaging stakeholders from different levels of the organization helps in creating a comprehensive change management plan that addresses diverse perspectives and needs.
3. Maintaining Transparency Without Overwhelming:
Rumors are your enemy. Get ahead of them by sharing information regularly to avoid their spread and the anchoring of bad impressions and resistance to change.
But, while transparency is vital, Zoe points out the importance of contextualizing information. Sharing too much information too soon can lead to confusion and anxiety. Instead, tailor the information to suit the audience's needs and provide it in manageable portions. This approach helps keep everyone informed and engaged without feeling overwhelmed.
Incentivizing Participation:
To encourage participation and commitment, Zoe highlights the effectiveness of incentives. For instance, offering monetary bonuses for achieving specific targets, such as zero unregistered stops in a shift, can motivate employees to embrace and support the change. Recognizing and rewarding efforts can significantly boost morale and engagement.
You can find a good application example of this in our SIP Manufacturing case study. There, Johnnie Green, Vice President of Operations at SIP Manufacturing, describes how the incentivization of good practices led to lower turnover rates.
“I wasn't really looking for a turnover rate to coincide with some of these metrics. But as we were able to use Factbird as a tool to train employees and help them monitor their own metrics, we saw a reduction in our turnover rate.
“This was directly correlated to the incentive program that we implemented. So we wanted to incentivize our employees by, you know, meeting their daily metrics, their shift target metrics, and their weekly metrics."
Bonus Tips for Successful Change Management
Here are some bonus tips on effective change management for you:
- Engage early and often: Start engaging stakeholders early in the process and keep them involved through regular updates and feedback sessions.
- Provide training and support: Ensure that all employees have access to the necessary training and support to adapt to the new changes.
- Celebrate small wins: Recognize and celebrate small milestones to maintain momentum and morale.
- Be patient and persistent: Change management is a gradual process. Be patient and persistent in your efforts to achieve long-term success.
- It’s not a one-shot game: One meeting or workshop is not enough. Change management is a continuous process of education, analysis, and improvement.
Conclusion
Effective change management is essential for the success of any new manufacturing initiative. As Zoe Karasch highlights, good communication, stakeholder involvement, appropriate transparency, and incentivization are critical components. By following these strategies, companies can navigate the complexities of change and achieve their desired outcomes.
If you would like to get more information on the topic of change management, we’ve already done a couple of podcasts touching on methods for introducing new technologies to shop floors, which you can check out here:
- The five-step Highway Solution for implementing new manufacturing systems.
- How to implement manufacturing software across multiple sites.
Remember to subscribe to Manufacturing Matters to get notified when the next episode is available on Spotify, Apple Podcasts, YouTube, Amazon Music, and other popular podcast directories.