Manufacturing Data Collection: How to Get Started in 5 Easy Steps.
Boost productivity and make informed decisions with accurate production insights with a simple, 5-step guide to effective manufacturing data collection.
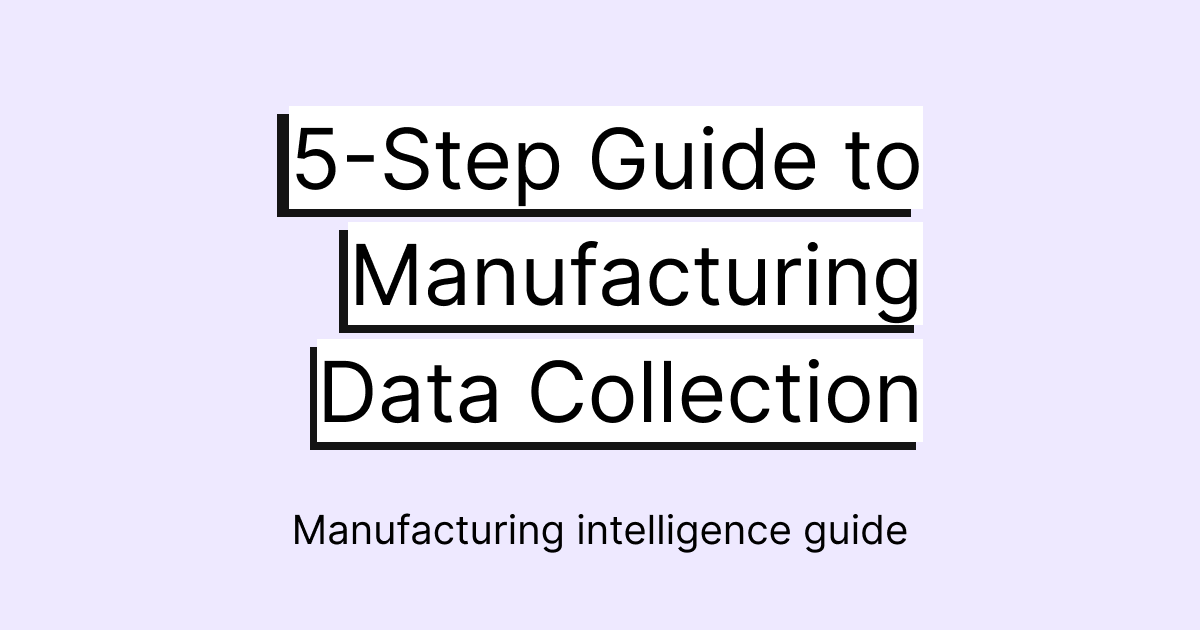
Manufacturers need accurate production data to be able to effectively change ways of working and increase productivity. Manufacturers who rely on intuition to make improvements will quickly lose ground to more effective businesses elsewhere.
Installing sensors and industrial IoT gateways that unobtrusively collect production data is now easy and cheap. And when you have a clear picture of reality through manufacturing data collection, convincing teams to change the status quo is a lot easier.
This article describes how you can quickly start to collect relevant data on production lines and quickly get to a state where you can make smart efficiency gains.
How do you collect manufacturing data?
It’s still common to see manual data collection on shopfloors globally. This is either done using pen and paper or on laptops and tablet computers. Here, operators record machine readings, register stops, record process results, or even manually count throughput. This approach is time-consuming, prone to human error, and does not offer real-time feedback. In saying that, it is still better than having zero manufacturing data collection efforts.
There is a clear shift to automatic data collection empowered by the Internet of Things (IoT) and advanced analytics for more efficient and reliable manufacturing data collection. A typical industrial IoT system has the following components:
- Sensors that convert physical phenomena into electrical signals.
- Edge devices and gateways that translate, store, and process the signals for communication with a network.
- Connectivity, such as cellular, LoRaWAN, Wi-Fi, and Ethernet, sends the data to the cloud.
- The cloud processes the data and then performs actions such as sending alerts.
- A user interface where people view and further analyze data.
Now let’s dig into the steps you’ll need to take for successful manufacturing data collection and shifting away from the old world of firefighting problems and struggling to increase productivity.
Step 1: Why do you want to collect data?
Here are some examples from our experience of why manufacturers typically start using Factbird to collect and analyze data:
- You have a feeling that a machine is bad; it seems problematic, but you can’t quite put your finger on what is going wrong.
- You realize you need to increase output and decrease costs due to pressure from customers, and/or you have pressure from labor shortages and material cost increases.
- You would like to better allocate human resources by knowing when certain processes or equipment need extra attention ahead of time.
- You’d like to move from reactive maintenance (putting out fires) to preventive and predictive maintenance, i.e., maintaining equipment before it breaks down and using technicians' time more efficiently.
- You have some data that you know you want to use already, but it’s not in a usable form. For example, you have PLC data, but it is not accessible for anyone to analyze.
The struggles that drive people to change the status quo of production and search for improvements cannot be understated.
Taking the leap and initiating change can feel like a risky and complicated proposition, and that’s why the next two steps help to simplify your path to change.
Step 2: What data would provide the most value?
Once you know your why, you can move on to the “what”: What kind of data should you collect to meet your goals?
1) Production performance
- Such as production counts and target vs. actual monthly production.
- Scrap and rework counts.
- Raw material consumption.
2) Machine uptime
- Uptime versus downtime (and its causes).
- Changeover duration.
3) Process parameters
- These influence both 1 and 2. Temperature and vibrations, for example.
- This data can also be used independently, e.g., to monitor the temperature in a cooling room.
- The real value of Manufacturing Intelligence comes from correlation analysis, i.e., measuring process parameters together with machine performance.
4) Utility consumption
- Monthly energy consumption.
- Monitoring the usage of electricity, water, gas, and compressed air.
The decision here depends on your industry, e.g., pharmaceuticals vs. food and beverage, the complexity of your production processes, and the state of your current manufacturing equipment.
Now let’s narrow the decision criteria down further to shorten your time to value for manufacturing data collection.
Step 3: Where would data deliver the quickest value?
Many Manufacturing Intelligence projects fail because they try to do too much from the outset. We often hear of manufacturers that have spent hundreds of thousands of dollars (and more) on building bespoke Manufacturing Intelligence Solutions that fail to get properly implemented.
Complexity and unexpected complications are the killers of projects. For example, manufacturers often have a variety of machine types at various ages (some are new, some are old, some are from one brand, some are from others), and you quickly realize rolling out a big IT project to cover all the machines and assets at once will be a massive undertaking.
Find out how Swedish Match increased OEE by 18% after implementing Factbird: Read the case story.
So, it’s a good idea to narrow your focus down to one area of interest. Run a proof of concept, start gathering relevant data immediately, shorten your time to ROI, and build a good case for expanding your Manufacturing Intelligence efforts.
You could begin by acting on a gut feeling about which machine might be the worst bottleneck.
- We typically recommend starting by collecting data from the machine you find the most problematic—the machine you hate the most. There's usually low-hanging fruit for improvement there.
- This focuses on improving individual machine performance (bottleneck) and enhancing the overall process efficiency.
If in doubt, in most cases, it’s best to start by measuring production performance.
- Collect data at the end of the production line to gain real-time metrics on the final output, such as the number of completed boxes.
- This focuses on the entire production line, treating it as a single, continuous process.
- Look at Overall Equipment Effectiveness (OEE) by tracking downtime (and causes) vs. planned production time and drill-down on what could give you the biggest production gains.
Here's a demonstration of how to measure Overall Equipment Effectiveness (OEE) with Factbird:
A great aspect of products like Factbird is that you can easily validate if the new system gives value through changes in OEE, showing you if your choice of moving to a data-driven approach has been worthwhile.
Step 4: How will you collect relevant data?
Now is the time to look at your production processes and figure out exactly what equipment you will need to collect data.
Sensors
Here’s an overview of processes and industrial sensors that can be used to collect relevant data:
- Production input and output monitoring can be done with proximity sensors, typically photoelectric (light) and inductive sensors, that monitor the number of items produced as well as scrap and items that need to be reworked.
- Packaging processes are a common cause of bottlenecks as they require multiple machines and complex actions. Sensors that accurately measure distances and positioning help reduce packaging problems.
- Bottleneck analysis uses video cameras to identify the root cause of stops by viewing timestamped videos.
- Condition monitoring of machines with vibration and temperature sensors that detect whether a piece of equipment behaves abnormally.
- Consumption monitoring of utilities such as electricity and gas to identify inefficiencies and reduce costs.
- Employee safety improvements by using video cameras to analyze what went wrong in the event of an accident.
For example, Omron E3AS proximity sensors are suitable for most cases. They can detect discrete items on the production lines as well as mechanical movements of equipment, which represent the produced items.
Otherwise, Factbird has invested time in building strong partnerships with sensor suppliers. We can connect off-the-shelf with any standard sensor, allowing us to find the right sensor for your specific application.
Connection options
Keeping it simple is the name of the game when you are starting out with manufacturing data collection.
A non-intrusive, plug-and-play data connection solution that takes sensor data and transmits it to the cloud using secure MQTT makes life a lot easier. If an industrial IoT gateway can be installed with minimal space, cable, and IT requirements and zero stoppages, then you’ll see a quicker and higher ROI.
You can capture data with industrial IoT gateways, for example Factbird DUOs, using three non-intrusive options:
- You can add extra sensors on a line (on a process) that connects to your industrial IoT gateways without any intrusion on existing OT/IT systems.
- You can copy a PLC signal in your control cabinet without interfering the PLC system. This is not intrusive to OT/IT systems as there’s no signal going back into the PLC system.
- You can copy signals from your existing sensors by splitting the sensor signal to your industrial IoT gateways. This is also a non-intrusive to your existing OT/IT infrastructure.
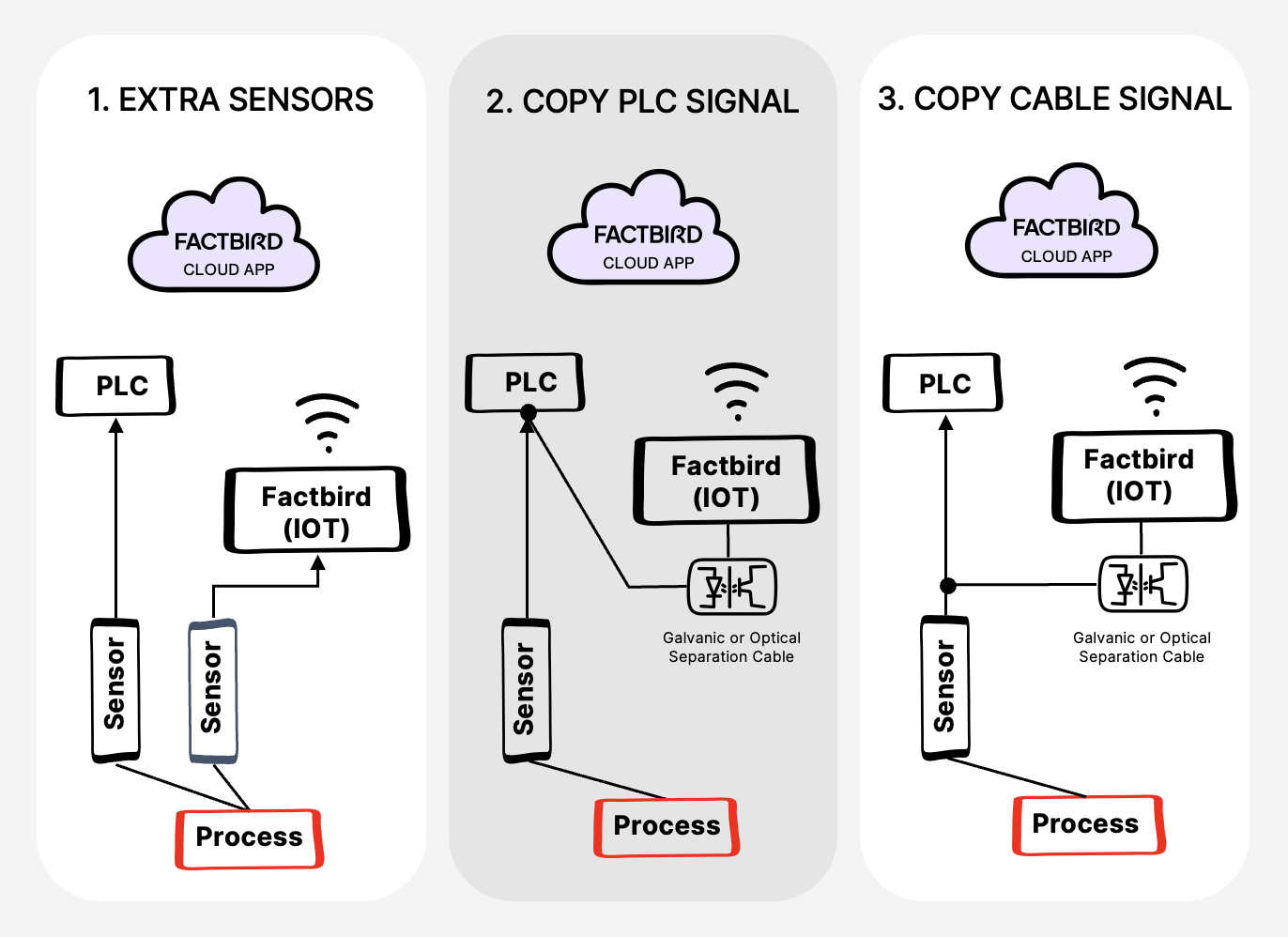
Once you have proof-of-concept, you can then consider whether you want to scale up your plug-and-play IIoT gateway solution, get data directly from a connected PLC, use Kepware, or use an MQTT connector.
Step 5: How does the device installation environment look?
The final prerequisite to successful manufacturing data collection is understanding the installation environment of the chosen production process you’d like to collect data on.
This will inform you about exactly what kind of hardware you will require to collect and connect data.
Connectivity options
Traditionally, connecting industrial machines requires Ethernet.
Mobile networks and Wi-Fi are becoming more popular as they become more stable in complex environments (thanks to Wi-Fi 6 and LPWAN, for example).
Ask yourself these questions:
- Is there factory Wi-Fi available for use?
- Do you have mobile coverage?
- Is there an Ethernet drop cable available?
After the proof-of-concept phase, you could consider private IIoT LTE networks to increase agility and reduce costs.
Dry or wet
Some manufacturing environments require heavy cleaning and harsh chemicals.
Ask yourself:
- Is the environment a wash-down environment?
- Do devices need to be ruggedized?
How Manufacturing Intelligence benefits teams
Relevant and collectible manufacturing data, such as throughput volume, scrap rates, energy consumption, cycle time, downtime, batch performance, etc., combine to help multiple departments at once:
- Maintenance: Data helps maintenance teams find the root causes of machinery malfunctions, moving teams from reactive to intelligent maintenance strategies.
- Operation team: Plant managers, supervisors, and operators go from half-remembered notes to accurate, automated, actionable data. Stop codes are easily tracked and visualized for greater efficiency.
- Finance: Thanks to accurate data, the financial department can draft more effective strategies to reduce production costs and produce better forecasts.
- Logistics: Logistics teams can better adapt to production flows and efficiently manage storage capacities when manufacturing data collection is handled in real-time and accessible to all areas.
- Management: The C-Suite has on-demand access to site- and company-wide levels. Good Manufacturing Intelligence Solutions like Factbird automate daily executive reports, shift reports, etc.
That is just a taste of where manufacturing organizations are headed thanks to better data collection on shopfloors.
Try Factbird’s plug-and-play manufacturing data collection solutions
That’s it. Once the above prerequisites are met (something that can often be figured out over one call), manufacturers can get started collecting data on shopfloors and increasing productivity.
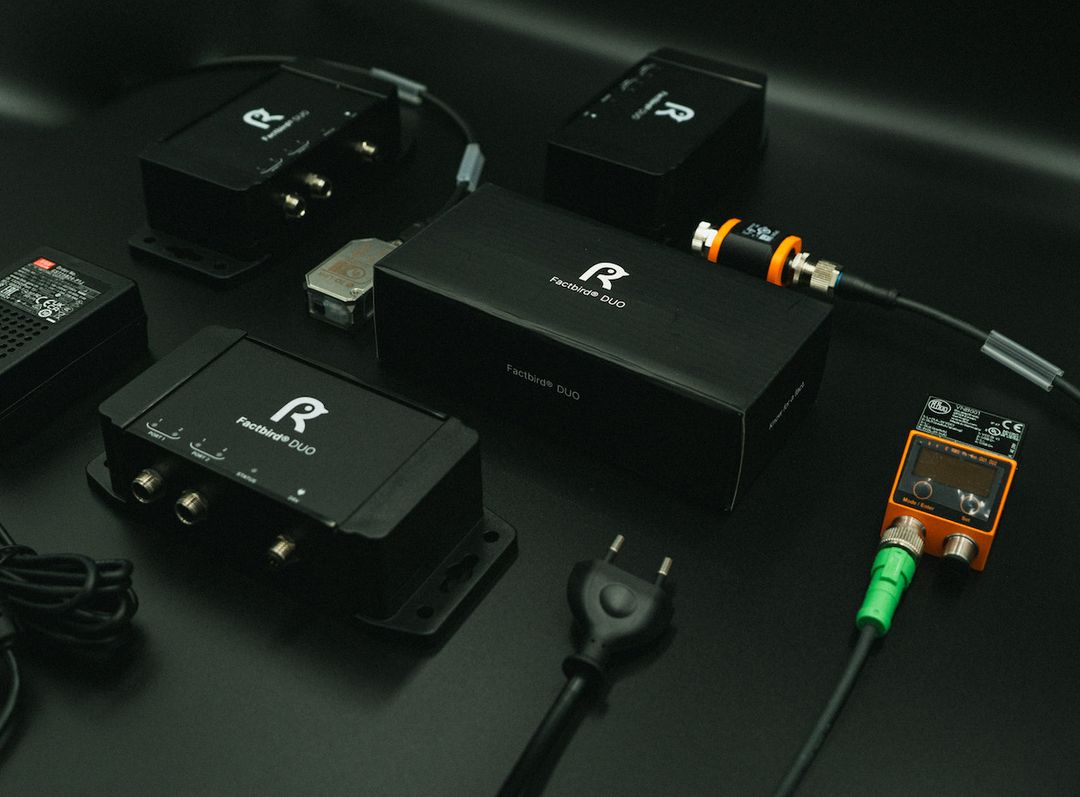
Easy setup, ease-of-use, and a clear path to operational excellence are things that Factbird offers that no one can compare. Check out our edge devices and gateways and begin your journey to data-driven performance.