Identifying and eliminating bottlenecks in your manufacturing process
In the competitive world of manufacturing, efficiency is key to staying ahead. One of the primary challenges is to identify and eliminate bottlenecks.
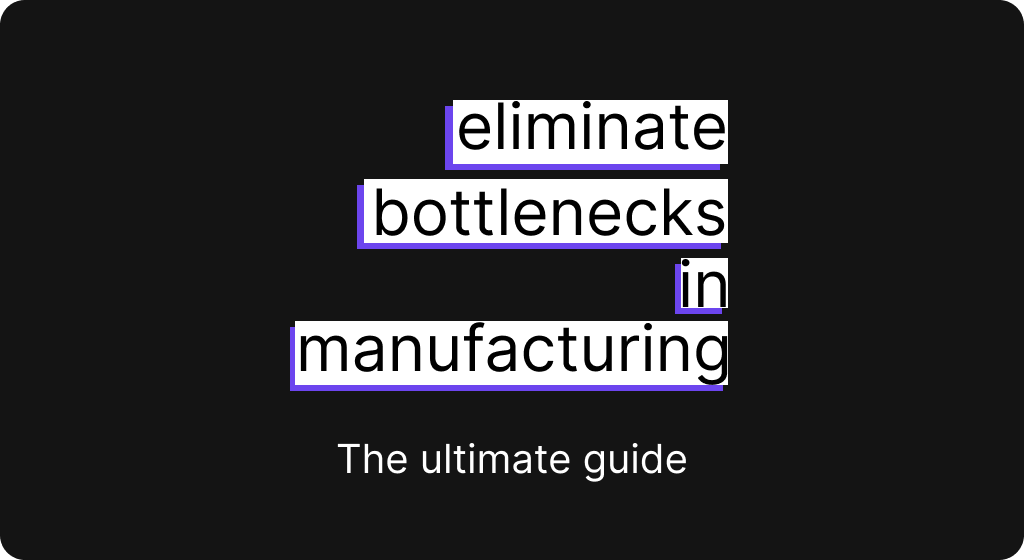
In the competitive world of manufacturing, efficiency is key to staying ahead. One of the primary challenges that manufacturers face is identifying and eliminating bottlenecks in their production process. Bottlenecks are points in the process where work accumulates, causing delays and reducing overall productivity.
In this blog post, we'll explore strategies for identifying and eliminating bottlenecks to optimize your manufacturing process.
Understand Your Production Process
Gaining a comprehensive understanding of your production process is the first step to identifying bottlenecks. To achieve this, map out your entire workflow, detailing each step, the time required for completion, and the resources involved. This visualization will provide a clear overview of your process and highlight potential areas of delay.
- Break down the process into smaller segments to analyze each step thoroughly.
- Identify dependencies between various stages, as these can contribute to bottlenecks.
- Document the capacity and limitations of your resources, such as machines and personnel, to understand their impact on your process.
Analyze Data and Metrics
Data analysis is essential for identifying bottlenecks in your production process. Collect and examine data on key performance indicators (KPIs) such as cycle time, throughput, work-in-progress (WIP), and machine utilization. These metrics can offer valuable insights into potential bottlenecks.
- Compare actual performance with planned performance to identify deviations and their possible causes.
- Track trends over time to identify recurring patterns that may indicate bottlenecks.
- Leverage advanced analytics tools and techniques, such as machine learning, to uncover hidden patterns in your data.
Observe Your Operations
Direct observation of your production process can reveal bottlenecks that may not be apparent in the data. Watch for signs of bottlenecks, such as:
- Work piling up at specific points in the process.
- Machines sitting idle for extended periods.
- Workers waiting for materials or instructions.
Additionally, look for inefficiencies, such as:
- Manual tasks that could be automated.
- Outdated equipment that slows down the process.
- Inadequate communication between departments or team members.
Address the Root Cause
Once bottlenecks are identified, it is crucial to tackle the root cause of the issue. Solutions may involve:
- Investing in new or upgraded equipment to increase capacity.
- Redesigning the process to eliminate unnecessary steps or dependencies.
- Improving worker training to increase proficiency and reduce errors.
- Implementing automation or digital technologies to streamline the process.
Involve your team in brainstorming solutions, and prioritize actions based on their potential impact on your production process.
Continuously Monitor and Adjust
Eliminating bottlenecks is an ongoing process that requires continuous monitoring and adjustment. To ensure the effectiveness of your improvements and prevent new bottlenecks from emerging:
- Regularly review your production process and KPIs.
- Conduct periodic audits to assess the efficiency and effectiveness of implemented solutions.
- Maintain open communication channels with team members to identify emerging issues promptly.
- Encourage a culture of continuous improvement within your organization.
In essence
Identifying and eliminating bottlenecks in your manufacturing process is essential for maintaining efficiency and staying competitive. By thoroughly understanding your production process, analyzing data, observing operations, addressing root causes, and continuously monitoring and adjusting, you can optimize your workflow and keep your manufacturing process running smoothly. Adopt a proactive approach to identifying and resolving bottlenecks, and you will be well on your way to a more efficient and productive manufacturing operation.