Data-driven manufacturing: Finn Hunneche on the importance of knowing the numbers
Manufacturing Matters Ep. 4
Finn Hunneche, Senior Partner, Emendo Consulting Group
Release Date: April 14, 2024
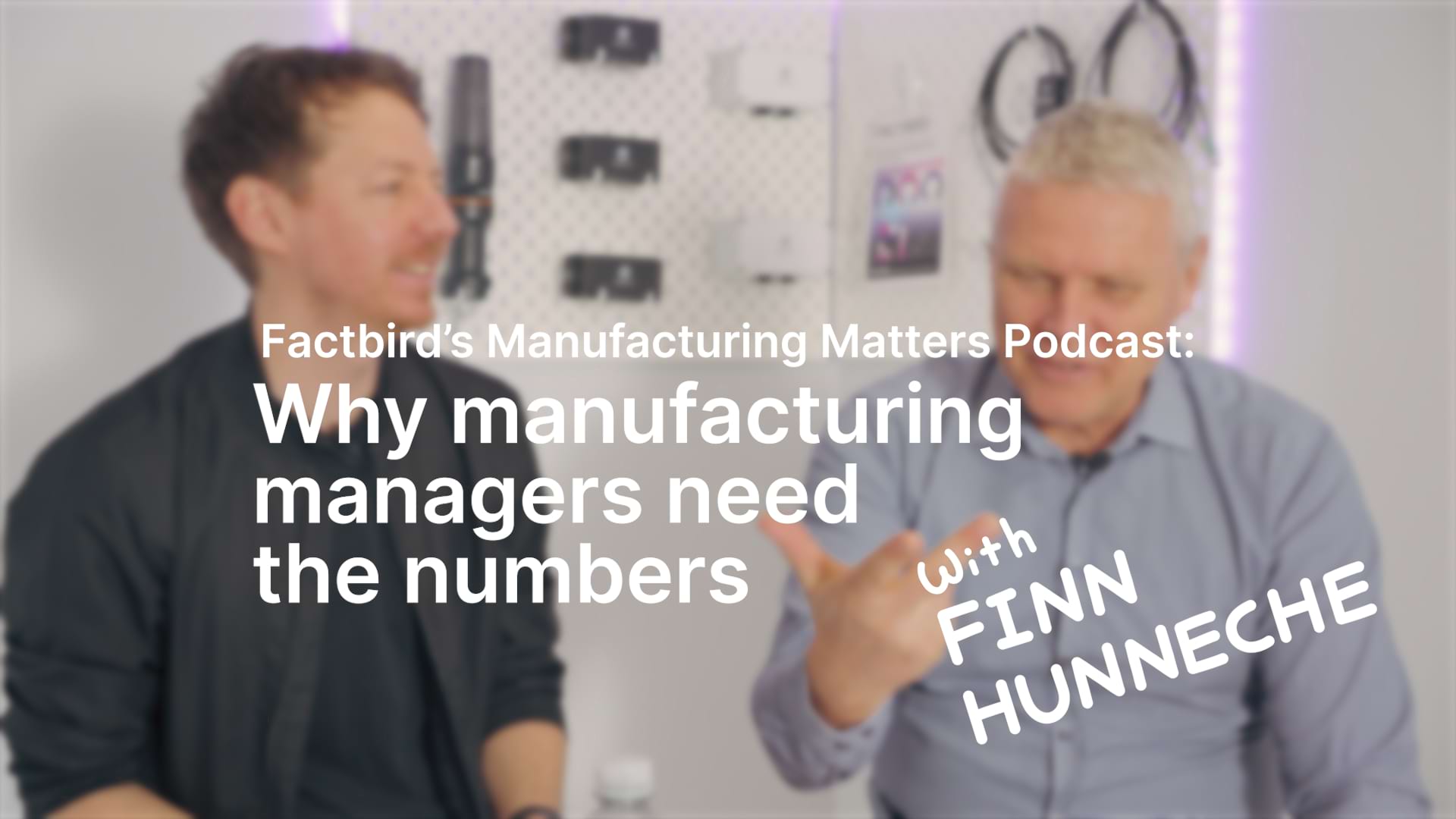
- There is more complexity than ever for manufacturing managers
- Finn’s advice for manufacturers is to make sure you get the numbers
- Start with small pilots, make mistakes, learn, and then expand
- Don’t be afraid to conduct experiments; if you do nothing, nothing changes
- Effective change requires good communication and buy-in form colleagues
In our fourth episode of Manufacturing Matters, I had the opportunity to talk to Finn Hunneche, a smart guy with over 35 years of experience in the manufacturing sector.
A start in software development eventually led him to Novo Nordisk, where he built a greenfield factory project, managed marketing and sales as General Manager in Turkey, and rose to be the Vice President of Global Support within Product Supply. Now, as co-founder and senior partner of Emendo Consulting Group and co-founder of Factbird, Finn continues to influence the manufacturing landscape and is someone who is very good at simplifying complex manufacturing problems.
With all this experience in mind, I asked him what his number one tip for manufacturers is. Here’s a summary of his answer.
The current challenges manufacturing managers face
Finn set the scene by laying out the three main challenges he sees that manufacturing managers are facing today.
The level of automation: There’s a growing number of automated systems (e.g. guided vehicles and automated machines) on production sites that come with new IT requirements. These new systems, while helpful, also make the manufacturing environment more complex.
The number of direct reports: Manufacturing managers have more direct reports than ever. It's not just upper management, it's also first-line support staff like supervisors who are too busy because of the high number of people to manage. In Finn’s opinion, if you really want to be efficient, the best setup is 6–8 direct reports, with a maximum of 15 or so. He is now seeing supervisors with over 30 or 40 direct reports at times, which leads to a lot of mistakes and inefficiency.
24/7 operation: It’s good that we are utilising the equipment we have more than ever, but, with so many shifts and different people coming on the site, who has the overview anymore?
So, even though manufacturing is more efficient, these three drivers make it significantly more difficult to be a manufacturing manager today than it used to be.
This is also the case for operators, as you need to have more skills to manage new systems and function well with less supervision.
Manufacturing managers need to have numbers
In the context of a more complex manufacturing environment, a strong focus on getting numbers makes sense.
“It’s impossible to survive in the manufacturing environment unless you have numbers.”
- Finn Hunneche
According to Finn, you need to convert all the opinions and missing know-how into numbers to be successful in manufacturing today. You need to have numbers on everything and have them visible to you in real-time so that you can make the right decisions.
It’s not enough anymore to walk the shop floor to ask people how things are going. It takes too long, and it’s not enough data.How should manufacturers get the numbers?
The point Finn is making is that you need to have a numbers mindset and be mindful that complexity will only increase.
“Insist on having numbers; that’s my number one tip.”
- Finn Hunneche
But thinking that you need to have numbers on everything will be a daunting proposition for those of you who have gone through a digitization project before.
Fortunately, you don’t need to have everything digital right away. In fact, you shouldn’t turn getting the numbers into a giant IT project.
As Finn says in the podcast, just collecting data with a pen and paper in a small area, making mistakes, and getting your proof of concept right is a good way to start. Once you’ve gone through a good pilot, you can scale from there.
Get buy-in from colleagues early
Another good point that Finn raised is that it’s important to get more people involved early. You don’t want it to be just “your numbers," but everyone’s. It can’t be overstated how important it is to get buy-in from people who are impacted early.
We have a good case study on Wozniak Industries that supports the need for team buy-in. In it, Lorne Day, their VP of Operations, says, “And it initially came across that this is something that Lorne wants to do, and that's the wrong thing. I probably presented it wrong.” which backs up Finn’s point here.
In the case study, Lorne continues, “This is a tool that we need to be successful, to keep these doors open. So this is our tool, not my tool. That's the culture you have to shift on. You have to get buy-in. It's all about the why. Everything's about the why.”
Perform experiments and communicate them well
So to sum up, successful manufacturing management is about the following three areas:
- The ability to understand that you need numbers.
- Getting the numbers.
- Making changes based on those numbers.
And the last part is the hardest one to do.
Having numbers by themselves will not do anything. It is only when you change behaviour that gains are made.
In Finn’s experience, companies can handle a lot of change before things start to break. Good manufacturing managers “are people who have this ability to dare to change and dare to make experiments.”
So having people who are willing to look at the data and act is vital for the success of organisations. You need people who can make changes and shift the way things are done.
According to Finn, you shouldn’t “be afraid of changing things; you can always change it back. It’s in the dialogue, the communication, and the trust of your team where you say, ‘Hey, we’re going to do an experiment, and if we fail, we will stay with what we have.’ But if we don’t allow experiments or if we don’t change anything, then the numbers will not improve.”
“You need to be super good at communicating, why are we doing this, what will happen, and why should you like it as a colleague.”
- Finn Hunneche
Throughout Finn’s career of hands-on manufacturing management and consulting, he doesn’t tend to meet people who have made too many experiments. Rather, where things have gone wrong, you tend to meet people who are bad at communicating why experiments are needed.And that’s that. If you’d like to know more, make sure you watch or listen to the podcast to get more in-depth detail.
Show notes
- You can watch and read Wozniak Industries full case study mentioned in the podcast here: Wozniak Industries Case Study.
- We briefly mention Claus from Banedanmark (Rail Net Denmark) and his take on change management. You can watch the webinar with him here: What Manufacturers can Learn from the Maintenance of Critical Infrastructure.
- If you would like to see the cool stuff that Finn and the team at Emendo Consulting are up to, I’d recommend following them on LinkedIn.
Remember to subscribe to Manufacturing Matters to get notified when the next episode is available on Spotify, Apple Podcasts, YouTube, Amazon Music, or your favourite podcast directories.