The road to Lights-Out Manufacturing: Insights from a Lean Improvement expert
In this article, we'll delve into how manufacturers can become digital winners and innovate in the competitive landscape.
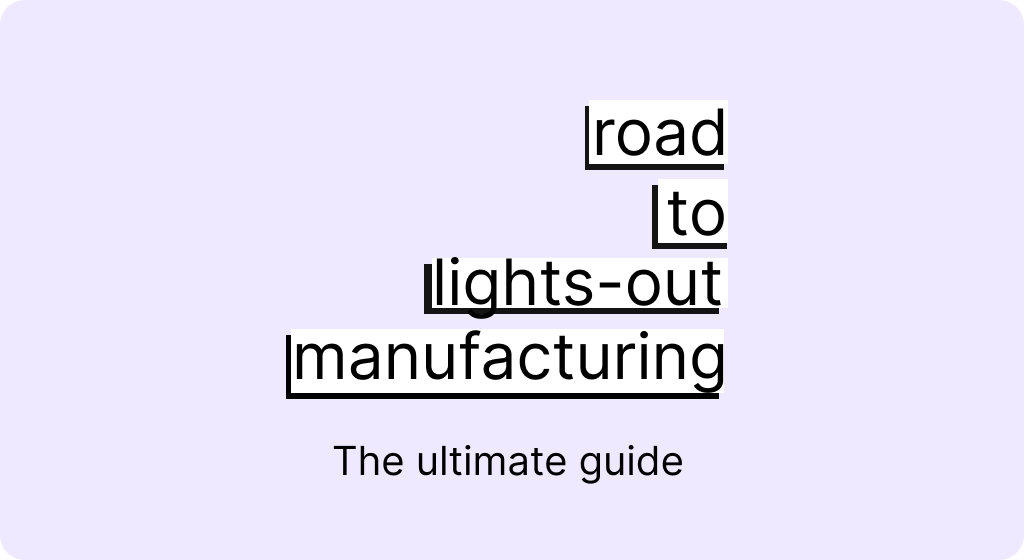
In this article, we'll delve into how manufacturers can become digital winners and innovate in the competitive landscape. We'll share insights from Line Pedersen, Partner and Senior Consultant at Emendo Improvement, an expert in lean improvement.
Lowering costs, increasing quality, and responding to changing customer demands are some of the biggest challenges faced by manufacturers. Those who want to succeed must embrace digitalization, gather data to improve and automate repetitive processes and move towards a clearly defined destination.
Winners are on a digital journey
Digital winners have a defined destination in mind, which is essential in deciding which tactics and strategies to use. This destination needs to be transparently labelled, not just from a goal-setting perspective, but also to align employees' efforts.
The end goal of the digital journey is the "Lights Out" phase, where products or services can be produced without human interference.
In today's ever-competitive manufacturing landscape, it is crucial to acknowledge the digital journey, define the route, and set sights on the final destination to stay ahead of the game.
If you haven't yet started your digital journey, this article can help trigger the process by asking the right questions and guiding you towards the digitalization of your manufacturing processes.
Defining the digital journey
To begin this journey, two critical questions must be asked:
- What does the journey look like?
- What are the critical success factors?
The outcome of the digital journey, the "Lights Out" phase, can be achieved by progressing through several key phases, which are part of the Digital Evolution. These phases include manual records, systems and reports, live data, signals, advice, predictions, adjustments, and finally, the "Lights Out" phase.
- Manual Records
- Systems & Reports
- Live Data
- Signals
- Advice
- Predictions
- Adjustments
- Lights Out - The outcome of our journey

However, advanced technology solutions are not the only answer to the digital journey. The cultural factor, which includes systemic and behavioral aspects, is crucial to the successful implementation of the digital journey. Without providing employees with the right infrastructure and mediums to access data, the data may lack validation, or it can be incomplete to measure.
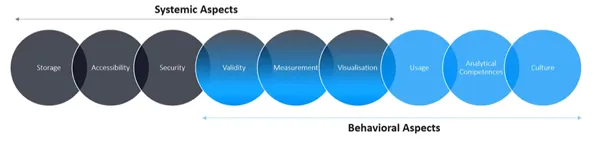
Why do we say that Systemic Aspects such as Storage, Accessibility, and Security are also part of the cultural factor? The reason for that is due to the infrastructure building the basis for the habit to create. We can coach our personnel in a culture of data-driven decisions. Still, without providing the mediums to access the data, such data may lack validation, or it can be incomplete to measure it.
Therefore, the cultural factor for the digital journey is a process in constant evaluation, as the conditions that make it possible can be altered and deter us from the proper path.
Now, let's explore phase-by-phase the components that shape the outcome of the digital journey.
Manual Records involves the traditional way of keeping data written in pen and paper in file cabinets, it is evident that this method has limited data and can be easily misplaced or destroyed. It is also not efficient from a time management perspective, leading to delays in producing each record.
System & Reports is the stage where a company starts to invest in IT to store documentation or manage the obtained data. Although some software implementations are added, a considerable downside of this stage is the tremendous administrative effort it requires, with human-error-prone situations that are foreseeable in times of maximum production. For operators, this is the starting point for getting data feedback that allows them to solve daily situations.
The next phase is the Live Data stage. We start building dashboards that showcase critical information to ensure the proper functioning capacity. Those dashboards get fed from hardware solutions, as variated as product line sensors, environmental sensors, security camera live footage, etc. It becomes fundamental to store the data and be able to retrieve it on a live basis. In order to avoid data stuffing for the personnel, the dashboards only display data relevant to the functions of the employees per section - meaning data feedback for what they can do anything about.
Signals is the phase in which we apply the extracted live data and turn it into indicators. Those signals are standards for how the operators should react. Hence, these signals act as limitations to the amount of data an operator has to memorize, becoming effective in standardizing procedures. Again, this represents a mindset shift as people need to trust the indicators and operate on their premises. At this point, it is essential to build the habit of logging the activities performed on the line. Such a process creates what is called historic data - an asset of vital importance for problem-solving scenarios or maintenance teams.
The application of historic data sets the ground for the Advice phase. Not just extracted data but procedures made to solve problems are used to build sophisticated models. These models aim to get the next steps to follow when a problem occurs, which is the initial phase in the link between machine learning and manufacturing. The pieces of advice give straightforward solutions, eliminating the human error factor.
Taking the modelling process to a more advanced stage is when we transition to the Predictions phase. It goes beyond manufacturing monitoring, and we are getting accurate predictions on what is bound to happen next based on vast amounts of analyzed data. Usually, a more significant number of sensors is required as the data demand increases. Rather than getting advice to solve a problem, operators get advice on how to prevent potential problems. These preventive measures are aimed at nullifying stop time for production lines.
Up to this point, automation is recommended but not required for the systems to function. Automation is required to move toward the Adjustments stage as the models built to predict behavior will interact with the equipment. If we need an adjustment, the model will tell the system to adjust in real time. Even when the automation process can be perceived as moving the operators far from the product lines, the company still needs them for control rooms. Operators are crucial for prediction model maintenance tasks.
The final stage is Lights Out. The human element is removed from production, but operators are assigned to work in the control room. Monitoring the production metrics and maintaining the prediction models is a task that only humans can handle.
How to Set the Success Criteria
In summary, to achieve a successful digital journey in manufacturing, it is crucial to define the success criteria that set the destination and the route toward the "Lights Out" state. Companies need to avoid isolated digitalization use cases and drive digitalization initiatives toward the end goal. It is essential to consider not only the systemic aspects but also the behavioral aspects of the journey, which are often neglected. With the right approach, businesses can optimize their manufacturing processes, reduce costs, and increase quality, giving them a competitive edge in the ever-evolving industry.