OEE formula: Factbird’s practical guide to calculating OEE
Let’s put together what we’ve learned about the OEE formula so far with a full OEE calculation example, including stop-cause categorization.
We’ll start by recapping the standard OEE formula, grouping stop causes into availability, performance, and quality losses and taking the product of them to get our overall total capacity utilization rate.
Then we’ll look at the waterfall method using the same data to get a breakdown of TCU, OEE1, OEE2, and OEE3.
Free Excel worksheet for calculating OEE
For this lesson, you can follow along with this free OEE calculator template in Excel:
Download the free Excel OEE Calculator Template
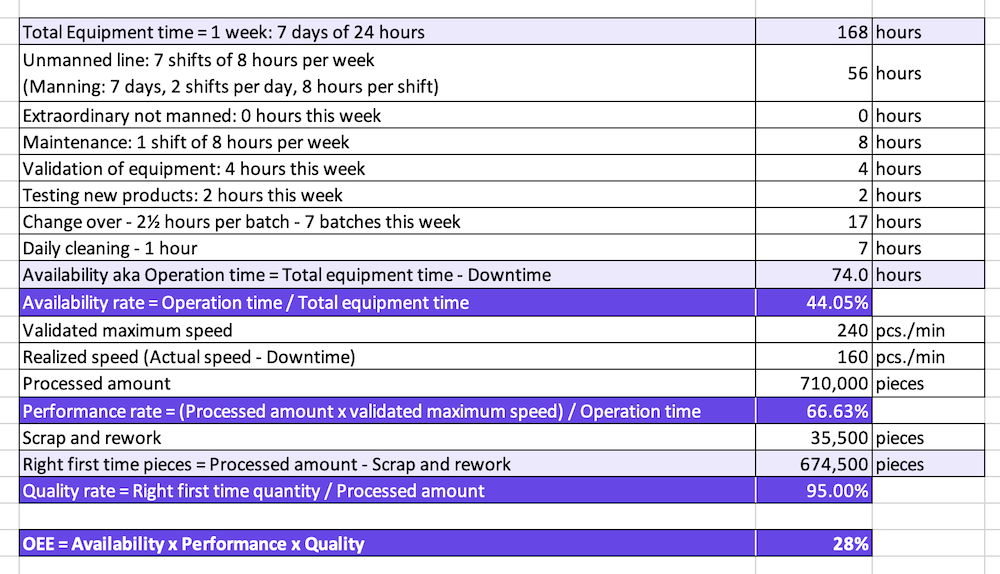
We hope you find it useful!
Let us know if you have any questions or recommendations for improvement by writing us at marcom@factbird.com.
What is the OEE formula?
The OEE formula is a simple equation used to measure how effectively manufacturing equipment or process is running. It’s defined as:
OEE = Availability × Performance × Quality
This standard formula, developed by Seiichi Nakajima, helps manufacturers identify production losses and drive continuous improvement.
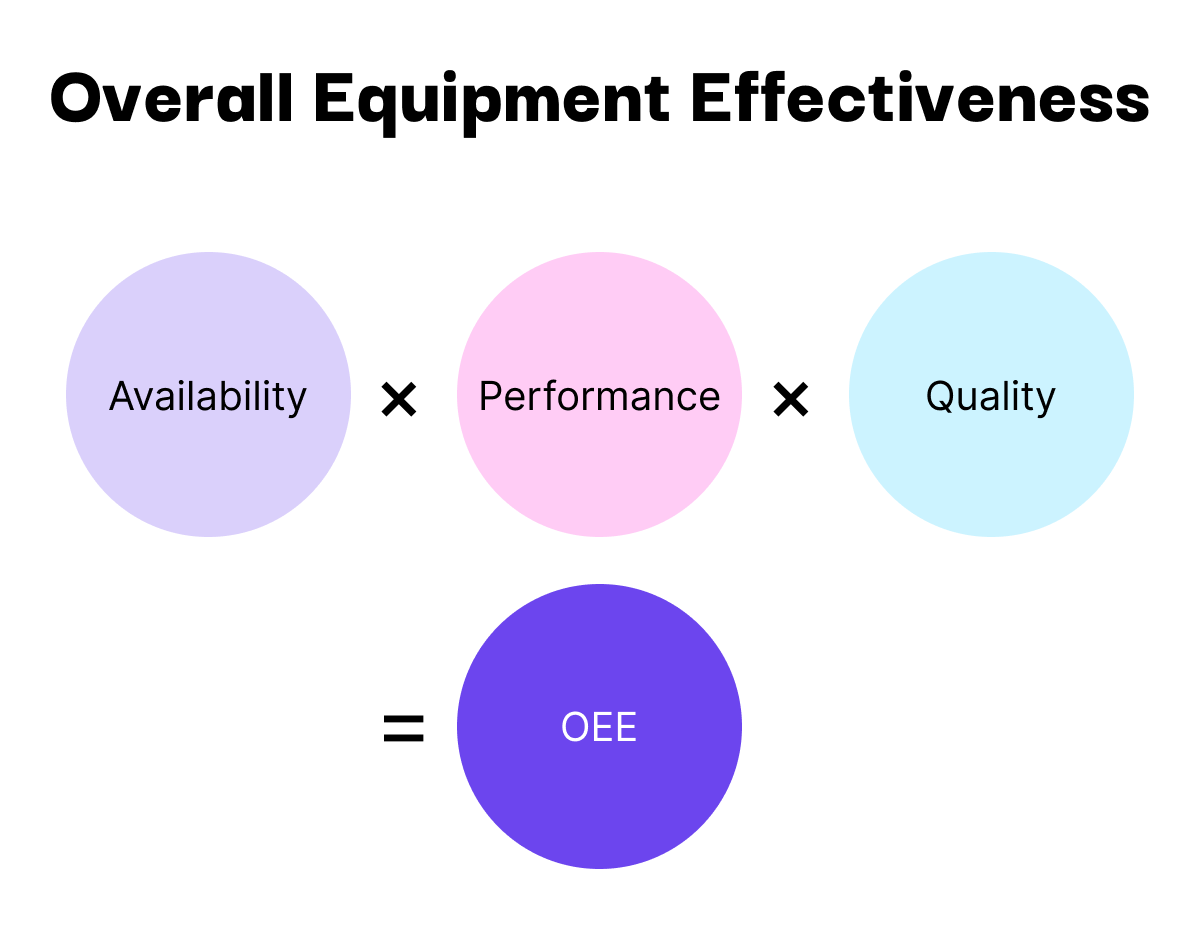
Now let's dig a bit deeper into how manufacturers use this formula to identify inefficiencis and reduce downtime with a thorough example.
How to calculate OEE (with examples)
At Factbird, we like to take into account all the time available for your equipment when making improvements, and not only the scheduled production time (aka Operation time). This means that availability losses include time where there is no activity at the line due to having no night or weekend shifts, for example.
So here, we are calculating Total Capacity Utilization (TCU), which is sometimes called Asset Utilization.
TCU = Availability x Performance x Quality
In short, TCU takes into account all available time for your equipment, while traditional OEE calculations only look at scheduled uptime.
Now let’s take a deep dive into that calculation using actual stop categories and downtime data.
Total Equipment Time
For this example, we will look at a week for a production line with a total equipment time of 168 hours.
Total Equipment Time = 7 days of 24 hours = 168 hours
This is the total amount of time our equipment is available for production for the time period.
Availability losses
Now, let’s calculate the availability losses.
First up, we will look at where there has been no activity at the line.
Throughout this week, the production line is manned for two, eight-hour shifts seven days a week, which comes to 112 hours.
- Non-scheduled hours = 168 - 112 = 56 hours
This gives us 56 hours where no production is scheduled.
We’ll keep extraordinary unmanned days at zero.
Now let’s look at non-production activities.
Here we have three stop categories:
- Planned maintenance = 8 hours
- Validation of equipment = 4 hours
- Testing new products = 2 hours
Our final group of availability losses we will look at are batch-specific non-production activities.
Here we have 24 hours worth of downtime:
- Changeover and setup = 17 hours
- Daily cleaning = 7 hours
Adding all of these availability losses up, we have lost 94 hours of availability.
- 56+8+4+2+17+7 = 94 hours
Subtracting our availability losses from our total equipment times leaves us with 74 hours of operation time.
- 168 - 94 = 74 hours
Then, by dividing 74 hours by our total equipment time of 168 hours, we end up with an availability rate of 44%.
Availability rate = 74 / 168 = 0.44
[CTA]
Performance rate and speed losses
Next up, are our speed losses. In this example, we can say our maximum speed is 240 pieces per minute.
- Validated maximum speed = 240 pcs / min
And the actual speed our line is running at on average is 161 pieces per minute.
- Actual speed = 161 pcs / min
Then, by dividing the actual speed of 161 by the validated maximum speed of 240, we have a performance rate of 67%.
Performance rate = 161 / 240 = 0.67
Now, you will often not know your actual speed over the period of measurement.
In the Excel template, we use the total processed amount to get the performance rate.
Performance rate = (Total processed amount / Validated maximum speed) / Operation time
Here, our total processed amount is 710,000 pieces and we convert our operation of 74 hours into minutes.
Performance rate = (710,000 / 240) / (74*60) = 0.67
As you can see, both methods of calculating the performance rate give us the same result.
Feel free to play around with this in the OEE Calculation Excel template.
NB It is easy to confuse the Ideal cycle time and Validated maximum speed. Remember that they are reciprocals, meaning "Validated maximum speed" = 1 / "Ideal cycle time".
"Ideal cycle time" is typically measured in minutes per piece or seconds per piece. A lower cycle time means faster production. Example: If it takes 0.005 minutes per piece to produce under ideal conditions, the ideal cycle time is 0.0050.005.
On the other hand, "Validated maximum speed" is measured as pieces per minute. Example: If the machine can ideally produce 200 pieces per minute, the validated maximum speed is 200 pieces/minute.
Quality losses
Finally, let’s add in our quality losses.
For this example, we will say we start with a batch size of 100,000 pieces.
- Batch size = 100,000 pcs
And let’s say we have 5,000 pieces of scrap in this 100,000-piece batch.
- Scrap per batch = 5,000 pcs
We then take our right-first-time quantity of 95,000 and divide that by our batch size of 100,000 to get a quality rate of 95%.
Quality rate = 95,000 / 100,000 = 0.95
Now, let's expand this out of the period of a week, something that many people will find more intuitive.
Over our 168 hour week (Total Equipment Time) with 74 hours of operation time, we had 7.1 batches and processed 710,000 pieces.
We also know that we had 35,500 pieces of scrap or rework, leaving us with 674,500 right-first-time pieces.
Quality rate = 674,500 / 710,000 = 0.95
Calculating TCU
Now that we know our availability, performance, and quality rates, we can use the OEE / TCU formula to calculate a 28% OEE.
And remember, at Factbird, we call this OEE score Total Capacity Utilization because we take into account all available time for your assets.
OEE = TCU = 0.44 x 0.67 x 0.95 = 28%
An OEE waterfall chart example
28% OEE doesn’t sound great, and if we know our data is reliable, we definitely want to do something about it.
But where should we start?
Thankfully, Factbird’s waterfall technique for breaking down OEE into TCU, OEE3, OEE2, and OEE1 helps us narrow down what to improve first.
Plotting the same data in a waterfall chart will give us a good overview of our equipment’s effectiveness.
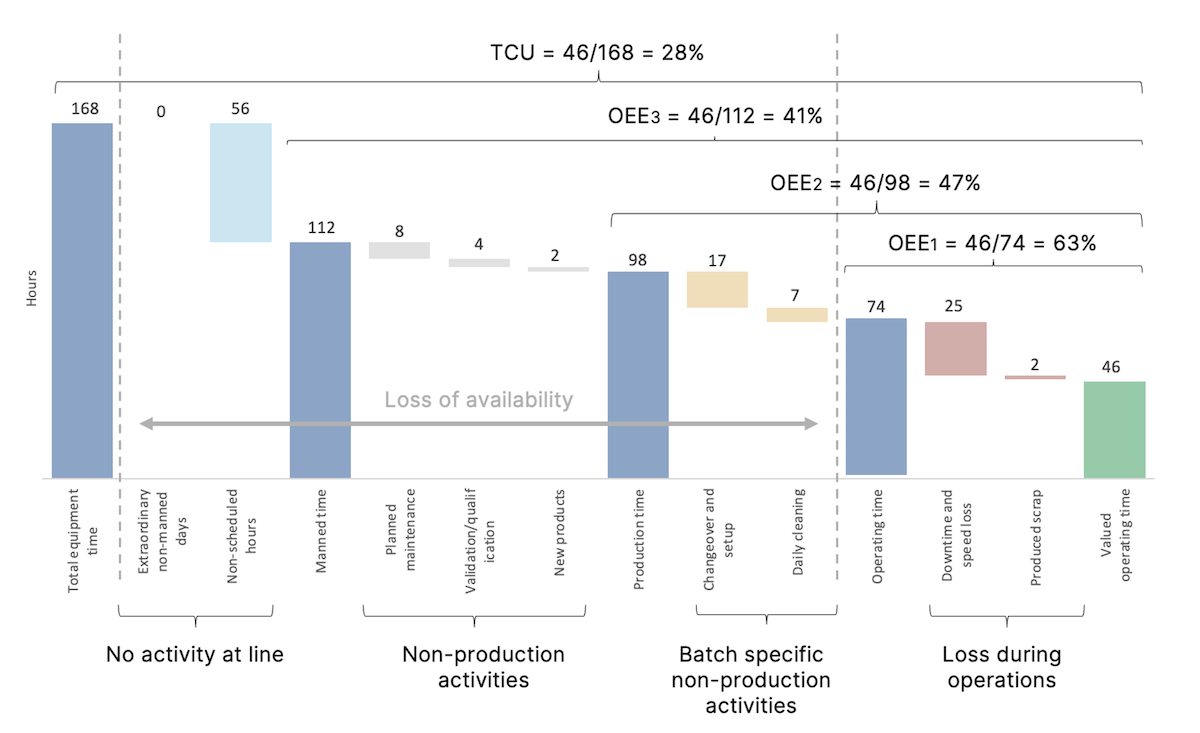
As you can see in the chart, we have four stop categories.
1. No activity at the line:
- Extraordinary unmanned days = 0
- Non-scheduled hours = 56
2. Non-production activities
- Planned maintenance = 8 hours
- Validation of equipment = 4 hours
- Testing new products = 2 hours
3. Batch-specific non-production
- Changeover and setup = 17 hours
- Daily cleaning = 7 hours
4. Loss during operations
- Downtime and speed loss = 25 hours
- Produced scrap = 2 hours
Note that "loss during operations" has been calculated as time losses in the waterfall calculation as opposed to unit-based scrap and quality losses.
This is a good example of different calculation methods leading to the same result.
However, it’s a lot easier to visualize where your losses are using the waterfall technique.
We can clearly see how stops take away time from our total equipment time potential, leaving us with 46 hours of valued operating time.
We also have a more granular view of OEE.
OEE1 = 63%
In most cases, companies are looking to have OEE1 at at least 75-80%, so this is low, and is something that should be addressed.
OEE2 = 47%
OOE2 includes changeovers, cleanings, etc., and often factories don't pay enough attention to these stop causes, taking for granted that the SLA is being met for changeovers and cleanings.
What we often find, is that there are some quick gains here. For example, when we start measuring OEE2, you will find that where there is a 30min SLA for cleaning, that they are often taking 37-40mins. Once companies have Factbird in and pay attention to these stop causes, it's common for there to be a lot of OEE uptick here.
OEE3 = 41%
OEE3 captures non-production time such as meetings and plant closures. You can decide whether or not there is potential to reduce meeting times, for example by having data more readily available on shop-floor performance dashboards.
TCU = 28%
This adds up to a total capacity utilization of 28%, which is low, but now that we have a more granular understanding of where the problems lie, we can quickly address our production problems.
Keep in mind that this is just an example of how to calculate OEE and that it’s not uncommon to have tweaks to how this is done from company to company.
And that’s it! You should now have a deep understanding of the OEE formula.
Join us in the next lesson on common issues with measuring OEE and best practices for implementing OEE.